Our production
Our aim is to develop high-quality solutions for your applications and to implement them efficiently and economically. In doing so, we focus on solutions that cause as little greenhouse gas emissions as possible. We do not shy away from challenges and are always breaking new ground together with you: with the help of our own tool shop, state-of-the-art machinery and technologies such as injection molding and thermoforming or thermoforming with IML (T-IML).

Injection molding
Thin-wall packaging
Spouts and closures
Screw caps
Injection molding is the most widely used process for the highly automated production of plastic workpieces by processing granulate. Complex shapes with different surfaces can be produced in almost any size. The manufacturing process can be fully automated. The raw material is melted in granulate form and injected into an injection mold under high pressure. After cooling, the article can then be ejected or removed using automation. We mainly use thermoplastics such as polypropylene (PP) or polyethylene (PE).

In-Mould-Labelling
Injection-molded packaging
Thermoformed packaging
With In-Mould-Labelling, plastic packaging is provided with a pre-printed plastic label during production. A robot positions the printed, thin plastic film in the mold. After the production process, the label and molded part form an inseparable unit with a continuous surface. The significant time and cost savings make the use of In-Mould-Labeling particularly economical. The process also scores points from an environmental perspective. With the same base material for the label and container, IML-decorated packaging can be recycled without any problems.
The advantages at a glance:
- Fully automatic control via camera system.
- Recycling with the same base materials.
- Captive component of packaging.
- Moisture and temperature resistant.
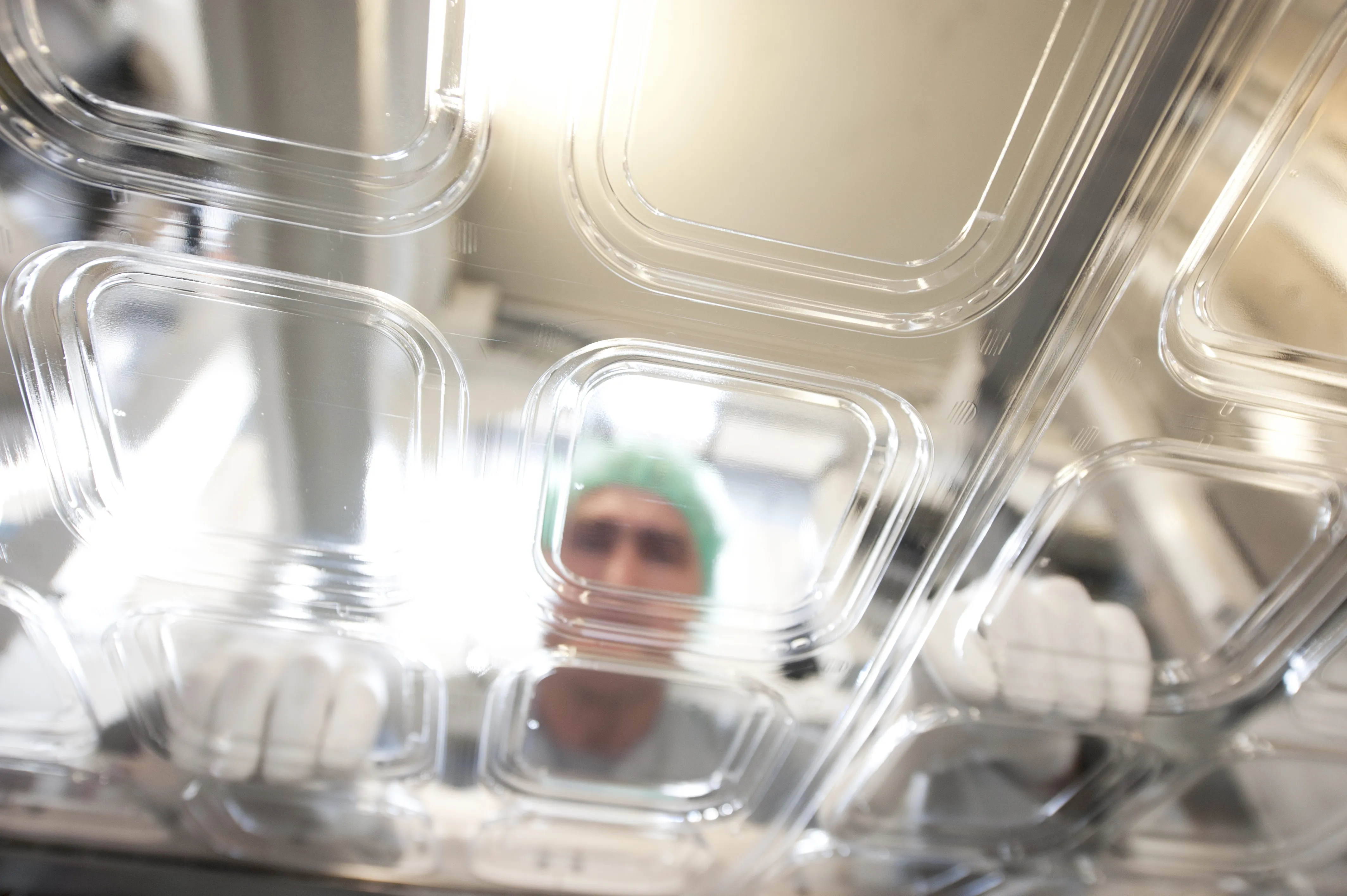
Thermoforming
Thin-wall packaging
Trays
In the thermoforming process, a plastic film is heated and shaped in the mold under the influence of a vacuum, cooled and punched out at the same time. The resulting packaging is then packaged fully automatically. The scrap skeleton produced during the process is fed back into the thermoforming process as a new raw material. We extrude the films on our own extruders. We produce our packaging on modern in-line and off-line systems with minimal use of materials and at the same time meet our customers' high requirements for stability and machine reliability. By using less material, we save on raw materials and reduce transportation costs along the entire supply chain.
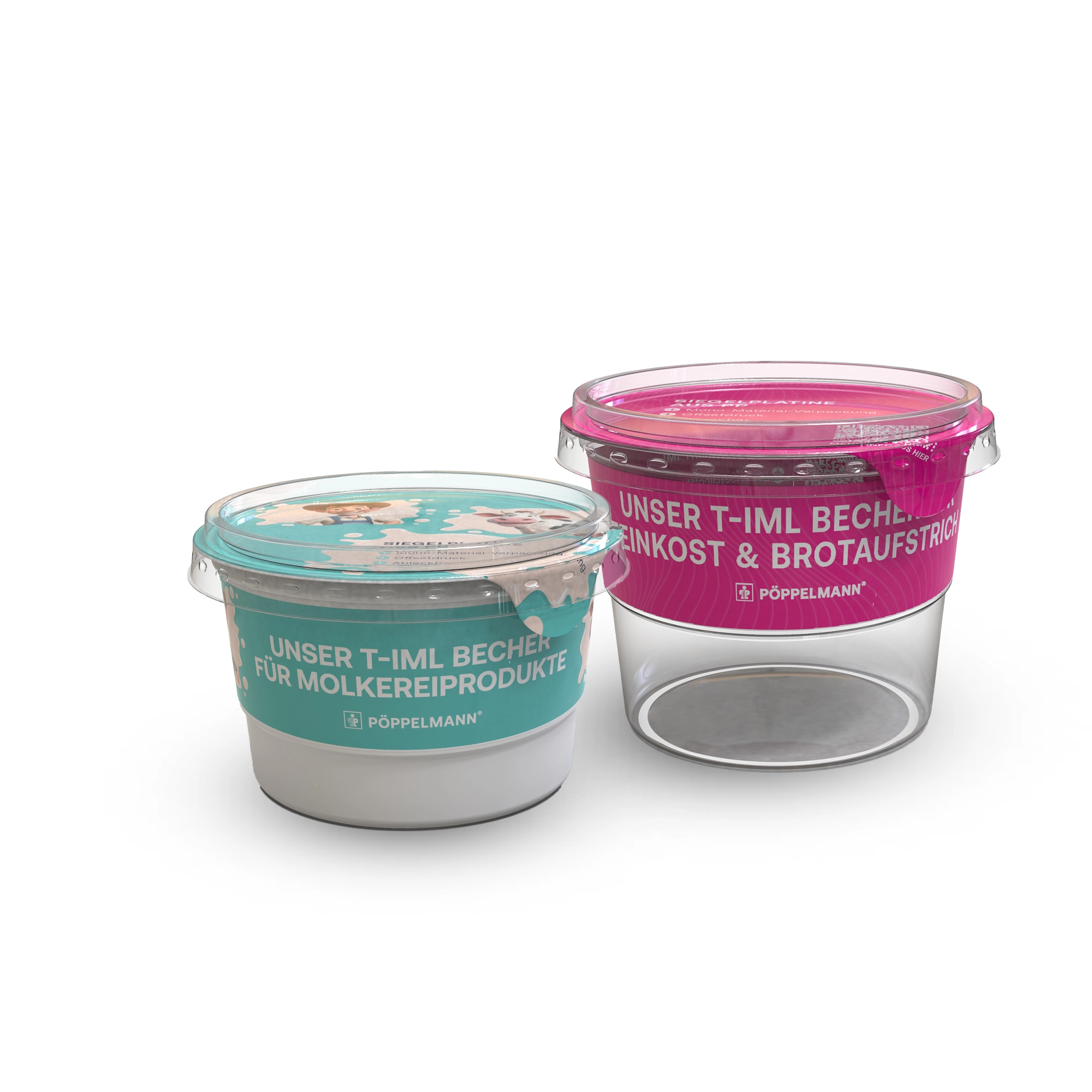
Thermoforming with IML
Thin-wall packaging
So far, this technology has only been used for plastic injection-moulded packaging. With the realization of a thermoformed dairy tub with IML, we combine our many years of experience in the areas of IML and thermoforming. The innovative and efficient T-IML process makes it possible to produce cups that are very light, as less plastic is used, and at the same time have a high-quality decoration. This decoration process is therefore the ideal basis for monomaterial packaging. Due to the same base material for the label and plastic article, IML-decorated articles are optimally recyclable.
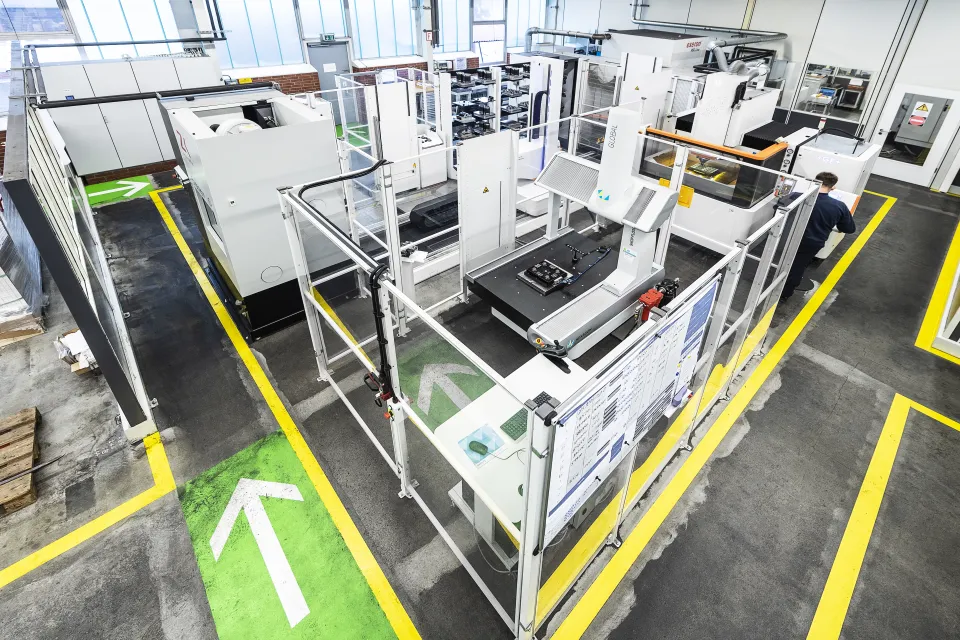
Moldmaking
Injection molds
Thermorming molds
Repairs / maintenance
We develop and produce sophisticated tools for plastics processing. Thanks to the wide variety of articles within the four Pöppelmann divisions, we produce molds for a wide range of applications. From thin-walled articles to complex functional parts in the automotive sector. The expertise of our more than 100 experienced specialists and our state-of-the-art machinery ensure the precision of our tools.
WHAT DO WE UNDERSTAND BY FUTURE-proof PACKAGING?
The sustainability assessment of packaging requires a holistic approach. This is because the product to be protected accounts for the largest share of the ecological footprint. Therefore, the most important task of packaging in terms of sustainability is safe product protection so that there is as little (food) loss as possible.
With eco-design, we implement product protection in the most resource- and climate-friendly way possible - the biggest lever is the circular economy.