Protective elements made from recycled plastic.
As part of our company-wide initiative PÖPPELMANN blue®, which aims to close material loops, we are developing sustainable protective caps and plugs. The protective elements are made from post-consumer recyclate (PCR), which is produced from used plastic products that have already gone through a complete life cycle. As our sustainable plastic caps and plastic stoppers are themselves 100% recyclable, they can be used to manufacture new caps and stoppers, as well as other plastic products, after use. This allows them to return to the material cycle.
The plastic content of our sustainable plastic caps and plastic stoppers consists of 100% PCR. We use the recycled material PCR polyethylene (PCR-PE) and PCR polypropylene (PCR-PP). All KAPSTO® products made from PCR-PE, PCR-PP and PCR-PE-HD bear the German government's Blue Angel eco-label, which is awarded for environmentally friendly products and guarantees that the products are made from at least 80% recycled material.
The NEW STANDARD.
SUSTAINABILITY IS SO EASY.
Under this claim, we have now expanded our standard range by a further 1,900 items made from 100% post-consumer recyclate and our new recycled blend in various colors. This is how we take responsibility for this and future generations.
PCR-PE, BLUE
100 % post-consumer recycled
contain our most sustainable protective elements, which therefore also conserve up to 100% of resources and can be fully returned to the material cycle after use. Our articles with such a high PCR content have been awarded the Blue Angel environmental seal since 2020.
PCR-PE / PE-LD
The recycling mix
is a mixture of predominantly post-consumer recycled material (PCR) and virgin material, which means that the protective elements have a significantly lower CO2 load compared to the variant made from virgin material. Thanks to the virgin material content, we are able to produce the items in a wide range of familiar colors despite the high level of sustainability.
Our sustainable KAPSTO® standard ranges made from recyclate in the plastic used:
Other sustainable protective elements
Added value of caps and plugs made of recycled plastic from KAPSTO®.
The use of recycled plastics reduces the need for primary and fossil resources
.The plastic content consists of up to 100% PCR
Certified with the Blue Angel
Sustainability through a closed cycle.
Our sustainable caps and stoppers made from recycled plastic are also 100% recyclable after use, provided they are disposed of in a suitable disposal system. One such disposal system can be direct recycling via Pöppelmann KAPSTO® itself. Please contact us if you are interested in setting up a closed material cycle with us.
We will then check individually whether this is possible for your case. You can see how the closed material cycle can work in the following illustration.
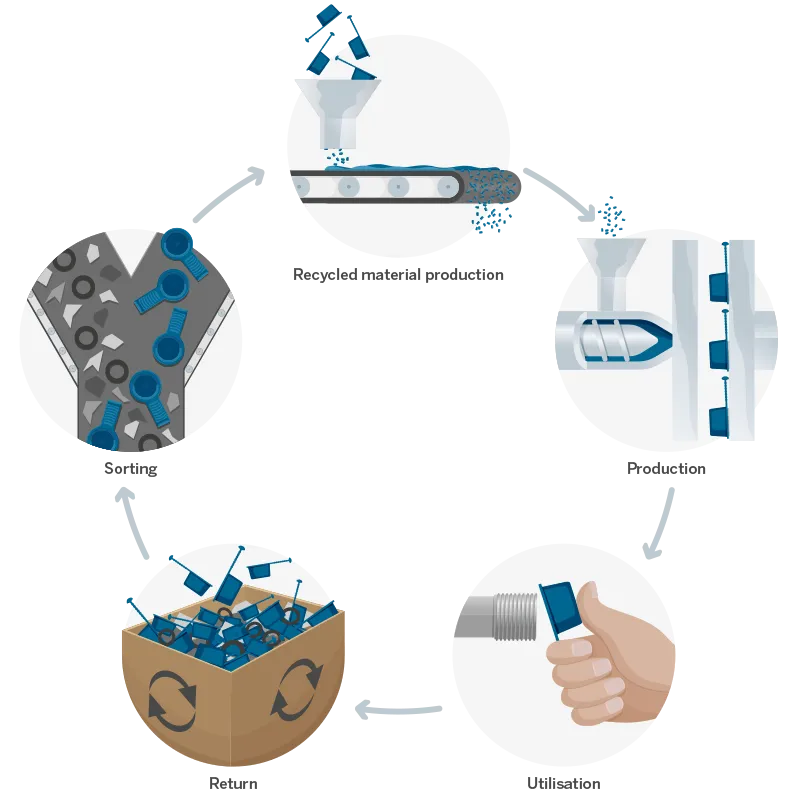
Our sustainable plastic caps in use at a name-brand car manufacturer.
Our plastic protective elements are mainly used in industrial production and protect sensitive and function-critical components from the ingress of dirt during production, storage and transport. The high-quality protective elements are then disposed of after a relatively short period of use. As sustainability is a key issue in our day-to-day activities, we presented our KAPSTO® plastic caps made from PCR-PE (polyethylene from post-consumer recyclate) to Mercedes-Benz AG in 2019. This marks the start of our cooperation.
Sustainability is not just a trend.
Even before the cooperation project, the plant had tried to reuse the caps, but failed due to the high quality requirements for the plastic caps. So the decision was made to recycle them - an optimal solution, as it turned out. This is because it preserves the high quality of the material, which continues to guarantee accuracy of fit, precision and safety, while at the same time closing the cycle. To this end, the caps are collected at the factory and picked up by Pöppelmann at regular intervals. They are then processed into recycled material from which new KAPSTO® plastic caps and plastic plugs are produced. The material cycle closes.
Now it's your turn
After the first successful projects, we want to launch further collaborations and firmly establish the topic of the circular economy in the industry. Because one thing is clear to us: this is the future of short-lived plastic products. Contact us if you would also like to close the loop in your company or have other ideas!
This is how we live responsibility in the Pöppelmann Group:
The sustainability report
Sustainable business practices have been the basis of our success for decades. In our decisions, we focus on the long-term added value of our actions. We believe this attitude is best described by the term „responsibility“. In our work, we assume this responsibility every day anew - for our employees and the quality of our products, for the natural resources of our planet and the region in which we are based. In this report, we set out how we live this responsibility in our company – and what goals we want and need to achieve.
Corporate Social Responsibility
Naturally, Pöppelmann takes responsibility: for over 30 years, we have been harmonizing ecological thinking and economic action - from conscious development to environmentally friendly production. We are certified according to DIN EN ISO 14001:2015 and EMAS. A holistic system for corporate social responsibility, compliance and risk management is currently being developed. And we voluntarily participate in the European Community eco-management and audit scheme.
Closed material loop with PÖPPELMANN blue®.
As a plastics processing company, we see it as our duty to make our products and processes as environmentally friendly as possible. Plastic is a recyclable material, yet less than half of all plastic waste in Germany is recycled. We want to increase this rate – to achieve this, we are working closely with our partners throughout the entire value cycle. With our PÖPPELMANN blue® initiative, we are aiming for closed material cycles. A product should be turned into a recyclate and the recyclate should be turned back into a product of the same quality.