Stories
Story
Le noir est out #pots de fleurs #recycle
En janvier 2025, le noir a été définitivement retiré du programme standard de TEKU®. Une étape importante. La gamme complète de produits est désormais entièrement recyclable : plateaux et pots, palettes de culture et pots de fleurs. Les matériaux précieux sont conservés pendant de nombreuses années. C'est une véritable économie circulaire qui réduit les émissions de gaz à effet de serre. Les clients bénéficient désormais d'une gamme de produits entièrement recyclables.
Il arrive qu'un sujet soit dans l'air et qu'une idée plutôt hasardeuse devienne soudain un gamechanger. Sven Hoping, directeur de la division TEKU®, se souvient : „C'était en 2017, lors d'une réunion en petit comité. La question s'est alors posée d'elle-même : Ne serait-ce pas cool que le matériel pour nos plantations provienne des sacs jaunes ?
A cette époque, TEKU® avait déjà plus de quarante ans d'expérience dans le traitement des matières recyclées pour la production de plants. Mais il s'agissait jusque-là presque exclusivement de résidus de production. Ces recyclats post-industriels (PIR) peuvent être réintroduits relativement facilement dans la production de nouveaux produits, presque comme des produits neufs. En effet, ils sont généralement propres et triés.
Il en va tout autrement des déchets de produits en plastique qui sont éliminés après usage &ndash ; comme les emballages par exemple. Ils finissent dans le sac ou la poubelle jaune et doivent être nettoyés, triés et analysés avec précision quant aux propriétés des matériaux avant d'être transformés en recyclats post-consommation (PCR). Mais pour pouvoir utiliser le PCR sans faire de concessions sur la qualité, il faut disposer d'un savoir-faire technologique et aimer le téléisme.
Pöppelmann fait bleu
Ça tombe bien. Car la pensée innovante, associée à la ténacité, au pragmatisme et à la compétence, fait partie de l'ADN des experts en matériaux et en processus chez Pöppelmann. Cela se manifeste à peine un an plus tard. En janvier 2018, TEKU® fait sensation au salon international de l'horticulture IPM. Des plantes bleues, fabriquées à partir de PCR et recyclables, sont présentées sur le stand. L'intérêt est énorme.
Avec cette présence au salon, Pöppelmann a établi de nouveaux standards pour la transformation durable des matières plastiques et s'est positionnée comme pionnière de l'économie circulaire dans le secteur. En interne également, au sein de l'entreprise : La même année, l'initiative stratégique d'entreprise PÖPPELMANN blue® ; est lancée. C'est là que les forces convergent pour développer, à l'échelle de l'entreprise, des concepts de produits pour l'économie circulaire. Maxime : le matériau plastique est bien trop précieux pour n'être utilisé qu'une seule fois
.
Mais pourquoi les boutons sont-ils bleus, pourquoi l'initiative d'entreprise PÖPPELMANN est-elle appelée blue® ? Ce choix de couleur et de nom a été inspiré par le modèle d'économie circulaire de la Fondation Ellen MacArthur. Il distingue deux cycles de matières premières : la couleur verte désigne le cycle biologique des matières premières organiques, la couleur bleue le cycle technique des matériaux tels que le métal ou le plastique, de la production au recyclage.
Ne voyez pas tout en noir
Il y a une deuxième raison à la coloration des pots. Dans le secteur de l'horticulture, les pots noirs sont considérés comme la meilleure option et la plus avantageuse pour une croissance optimale des plantes. L'opacité est un facteur essentiel. L'inconvénient : les détecteurs proche infrarouge des installations de tri des systèmes duaux ne peuvent pas suffisamment reconnaître les plastiques noirs. C'est pourquoi les plantes noires se retrouvent le plus souvent avec les restes d'emballages non triables &ndash ; et donc, après une seule utilisation, dans la valorisation énergétique.
Cela montre clairement que l'utilisation de matériaux recyclés n'est que la première étape sur la voie de l'économie circulaire. Pour boucler la boucle, le produit lui-même doit être recyclable. C'est pourquoi le choix des couleurs joue un rôle important. Et c'est là que réside le défi de remplir toutes les conditions pour une croissance optimale des plantes et les exigences de processus dans les entreprises horticoles, même avec des pots colorés.
Une étroite collaboration entre les départements afin de rassembler l'expertise de toute l'entreprise a toujours été la réponse de Pöppelmann à des défis tels que celui-ci, avec des améliorations constantes de la technologie et des processus de production. En 2021, TEKU® présentera les plantes Circular360, respectueuses des ressources, dans une large gamme de couleurs tendance, fabriquées à partir de PCR et recyclables dans les sacs jaunes, opaques et résistantes aux UV.
Sans noir systématiquement durable
En renonçant aux matières plastiques noires dans son programme standard, TEKU® se positionne désormais résolument en faveur de la protection du climat et de la préservation des ressources. Le directeur des ventes de TEKU®, Arno Zerhusen, et l'Area Sales Manager, Dirk Moormann, sont fiers que cette étape ait été franchie. Notre objectif était et reste de répondre aux exigences élevées de nos clients en matière de qualité et d'efficacité, tout en protégeant davantage le climat et en préservant les ressources grâce à nos produits", déclare Arno Zerhusen.
Ce n'est d'ailleurs possible qu'avec des flux de recyclage propres. Dirk Moormann explique comment TEKU® dirige le bon matériau dans les ateliers de production : „Les fournisseurs sont tenus de fournir des matières premières pures et recyclables, qui n'introduisent pas de composants non recyclables, comme des matériaux noirs, dans le processus de recyclage. Les clients peuvent être sûrs que nos produits ont été fabriqués avec ces matériaux. Des certifications indépendantes telles que l'Ange bleu, cyclos-HTP et RecyClass garantissent le respect de normes environnementales strictes.
Simon Lambrecht, chef de produit au sein du développement TEKU®, évoque les prochaines étapes : „Nous n'allons pas en rester là. En collaboration avec nos partenaires, nous voulons exploiter d'autres sources de matériaux afin de maintenir les matières premières précieuses dans le circuit. Nous avons besoin de partenaires qui poursuivent le même objectif. Par exemple, TEKU® est en contact étroit avec ses fournisseurs pour trouver, tester et mettre en circulation des matériaux appropriés.
La valeur ajoutée de cet engagement pour la protection du climat et la préservation des ressources se mesure en chiffres : L'empreinte carbone d'un pot recyclable PCR est réduite de 25% par rapport à un pot en matériau neuf.
Le directeur de la division Sven Hoping estime que la voie empruntée en 2017 est confirmée sur le marché, tant du point de vue de la durabilité écologique qu'économique. Il déclare : „De plus en plus d'entreprises du ‚grand secteur’veulent également rendre leurs processus de production plus durables. C'est là que nous intervenons en soutenant l'horticulture professionnelle avec des produits modernes qui permettent une croissance optimale des plantes tout en préservant l'environnement et le climat.“
Story
Economie et durabilité en harmonie #emballage #5p
Economie et durabilité en harmonie #emballage #5p
Nous sommes convaincus que le succès économique et la durabilité ne sont pas contradictoires. Au contraire, nous considérons que l'association de ces deux aspects est la clé d'innovations porteuses d'avenir, à la fois rentables sur le plan économique et respectueuses de l'environnement.
Un exemple remarquable est le nouveau design d'un pot de fromage blanc aux herbes de marque de distributeur, développé par notre division FAMAC® ; dans le cadre d'un projet commun avec le groupe DMK.
.
Le succès de ce projet montre de manière impressionnante comment des adaptations intelligentes de solutions d'emballage éprouvées permettent d'économiser de précieuses ressources. Le jury du Prix allemand de l'emballage 2024 a également été convaincu par la nouvelle conception du pot de fromage blanc, qui réduit les matériaux : DMK et Pöppelmann FAMAC® ; ont été récompensés pour ce projet innovant lors du salon professionnel Fachpack à Nörnberg dans la catégorie rentabilité.
Notre vision holistique repose sur cinq questions d'égale importance. Lisez comment nous y avons répondu pour cet emballage :
Sommes-nous en train de résoudre efficacement un vrai problème ?
Le gobelet à fromage blanc ürevisité devait conserver la fonctionnalité existante, mais être conçu de manière à économiser les ressources. Le résultat : grâce à des adaptations constructives dans la conception de la paroi du gobelet, la stabilité de l'emballage est maintenue, même avec une utilisation réduite de matériaux.
Cette solution est-elle rentable pour nous et nos partenaires ?
Une utilisation moindre de matériaux signifie non seulement des coûts de production réduits, mais aussi une logistique optimisée et donc des avantages économiques pour tous les participants, y compris une réduction des frais pour les systèmes duaux. Le jury du Prix allemand de l'emballage a souligné que la fabrication nécessite 20 pour cent de plastique en moins (polypropylène). De plus, 50 pour cent de gobelets en plus tiennent dans une boîte de transport réutilisable, ce qui augmente considérablement l'efficacité de la logistique. Grâce à la réduction de l'espacement entre les piles, les magasins des installations de collecte des déchets peuvent contenir 50 % de gobelets en plus, ce qui améliore également l'efficacité du processus de collecte. ;
A-t-on un processus qui fonctionne rapidement, efficacement et en toute sécurité?
L'adaptation du procédé de moulage par injection garantit que le scellage du gobelet après son remplissage se déroule sans problème malgré l'épaisseur de la paroi. Ce résultat a été obtenu grâce à des entretoises placées sur les parois intérieures du gobelet, qui compensent la pression d'écrasement. Elles ne sont pas visibles pour le consommateur, mais elles ont un impact important : ce remaniement du design permet d'économiser plus de 20 % d'émissions de GES par rapport aux alternatives typiques du marché.
&Une telle solution convainc toutes les parties prenantes et les acteurs tels que les clients et les consommateurs ainsi que les associations intéressées?
L'utilisation réduite de matériaux n'a pas d'influence négative sur l'utilisation pour le consommateur, mais augmente l'attractivité de l'emballage durable. Le jury du Deutscher Verpackungspreis (prix allemand de l'emballage) a fait l'éloge de ce projet comme étant une histoire à succès passionnante et a particulièrement apprécié la collaboration partenariale entre DMK et Pöppelmann FAMAC®.
Cette solution est-elle öco-efficace?
En économisant le plastique, le nouveau gobelet contribue activement à la réduction des émissions de CO2. DMK avait déjà supprimé le couvercle traditionnel pour certains produits au fromage blanc, ce qui avait permis d'économiser des quantités considérables de plastique. Avec l'optimisation du gobelet moulé par injection, une nouvelle étape importante a été franchie dans la préservation des ressources.
Cet exemple montre que les solutions de produits durables ne sont pas seulement possibles, mais aussi économiquement viables. Avec un travail acharné, de la minutie et la volonté de changer, nous développons des solutions qui convainquent le marché et contribuent en même temps à la protection du climat.
Story
Durabilité dans la technologie médicale:
Un nouveau design réduit les émissions de GES #pharma-medical #optimisation de la logistique
Durabilité dans la technologie médicale:
Un nouveau design réduit les émissions de GES #pharma-medical #optimisation de la logistique
Les personnes actives dans le domaine de la technologie médicale doivent répondre aux exigences les plus élevées. En effet, dans ce domaine, des vies humaines sont souvent en jeu. Mike Landwehr, directeur adjoint des ventes chez FAMAC Pharma-Medical, souligne : "La sécurité et la performance sont bien entendu prioritaires.
Cela signifie qu'il n'est pas possible de modifier rapidement un processus de fabrication ou de remplacer un matériau. L'utilisation de matériaux recyclés n'est pas non plus possible dans de nombreux cas. Néanmoins, FAMAC Pharma-Medical relève le défi de l'utilisation durable des ressources
.
Avec succès. C'est ce que montre l'exemple de la collaboration entre FAMAC Pharma-Medical et Drägerwerk AG & ; Co. KGaA pour le développement de pièces de boîtier pour un filtre de système d'aération HME. Ces filtres minimisent le risque de transmission d'infections en filtrant les virus et les bactéries lors de la ventilation clinique et en humidifiant l'air respiré par les patients. Ils sont utilisés en anesthésie et en soins intensifs.
.
Lors du développement du boîtier de filtre respiratoire, l'équipe FAMAC a dû tenir compte de plusieurs exigences du client. Parmi celles-ci, la conception carrée du design au lieu de la forme ronde précédente. Mike Landwehr : „Nous avons pu combiner cette exigence avec d'autres améliorations. Nous avons été convaincus par notre proposition de faire rentrer plus de pièces dans un emballage.“ Maintenant, la nouvelle variante permet d'empiler les pièces en économisant de la place et donc d'optimiser nettement la logistique, le transport, le stockage et l'emballage. De plus, la forme carrée du matériau filtrant permet de réduire les chutes de matériau
.
Le concept d'éco-conception est au cœur du travail de toutes les équipes de développement de Pöppelmann. Ce concept se caractérise par une vision globale des exigences &ndash ; et par la volonté d'aborder les tâches sous différentes perspectives et de les repenser ; l'impact environnemental d'un produit est pris en compte tout au long de son cycle de vie et maintenu aussi faible que possible
.
Comme dans ce cas : les exigences du client ont pu être combinées avec d'autres avantages &ndash ; qui contribuent tous à la réduction des émissions de gaz à effet de serre. Il s'agit notamment de l'utilisation de résidus de matériaux issus du processus de production dans la transformation des matières plastiques („sse&ldquo ;). Ce qui finissait autrefois dans les déchets plastiques est maintenant refondu et réutilisé.
Aujourd'hui, le nouveau design du boîtier présente encore plus d'avantages: Le procédé de moulage par injection utilisé dans la fabrication permet de réduire de 6% les émissions de GES par rapport à la quantité annuelle produite.De plus, la forme carrée permet un empilage peu encombrant des pièces et donc une nette optimisation logistique de l'emballage, du stockage et du transport : alors qu'auparavant, une palette pouvait contenir 4 800 pièces en vrac, elle en contient désormais 7 392. Nous avons ainsi pu réduire les émissions de GES dans le domaine de la logistique de 3,3 tonnes de CO2e &ndash ; ce qui correspond à 32 pour cent ; toujours par rapport à la quantité annuelle de production.
La nouvelle conception des filtres respiratoires ne convainc pas seulement en matière de préservation des ressources : Dräger a été récompensé par un Red Dot Design Award pour ce produit déjà introduit sur le marché. Le jury a déclaré : „Lors de la conception de ces filtres de protection respiratoire, une grande importance a été accordée à la protection des patients et du personnel médical.“
.
Plus d'infos sur le site de Pöppelmann :
Exemple pratique d'optimisation de la logistique-Dräger
Story
En route à vitesse turbo vers l'économie circulaire #automobile #recycle
En route à vitesse turbo vers l'économie circulaire #automobile #recycle
Le passage à une véritable économie circulaire fait partie des enjeux stratégiques décisifs, y compris dans l'industrie automobile. Pendant longtemps, on a considéré qu'il était techniquement irréalisable d'utiliser des matériaux recyclés post-consommation dans la construction automobile. Mais nous y sommes parvenus. Et nous sommes prêts à mettre en œuvre, en collaboration avec nos clients, les dispositions légales prévues par l'UE pour l'utilisation de matériaux recyclés dans la construction automobile (directive sur les véhicules en fin de vie).
Frank Schockemöhle, directeur de la gestion technologique chez Pöppelmann, se souvient encore très bien d'une conférence en juin 2022 : „J'étais invité à donner un aperçu de notre travail sur le thème de l'utilisation de matières recyclées dans la construction automobile. L'orateur précédent a conclu son exposé par ces mots : ‚Il faudra encore attendre dix ans avant que les matériaux post-consommation ne soient utilisés dans les voitures.&lsquo ; J'ai alors pris le micro et j'ai pu dire : merci beaucoup. Mon sujet est que nous sommes déjà en série.“
Car à cette époque, la division K-TECH® de Pöppelmann s'occupait déjà depuis longtemps de la conception et du développement de pièces automobiles pour l'économie circulaire. En 2018, l'initiative stratégique de durabilité PÖPPELMANN blue® a été lancée. Dès lors, les thèmes de l'économie circulaire et de la préservation des ressources ont donné le ton à l'échelle de l'entreprise. Maxime : „Le plastique est un matériau bien trop précieux pour être utilisé une seule fois.“
Les matières plastiques recyclées post-consommation (PCR), fabriquées à partir de produits jetés après usage, tels que les déchets recyclés des sacs jaunes, étaient désormais au centre de l'attention.Avant même le lancement de PÖPPELMANN blue®, TEKU® fabriquait depuis plus de 50 ans des plants à partir de recyclats post-industriels (PIR), c'est-à-dire de résidus de production. Ce savoir-faire a été le point de départ, après la création de l'initiative d'entreprise, de la conversion progressive de la production de TEKU® aux recyclats post-consommation.
C'est ainsi qu'un effet Pöppelmann particulier agit comme un accélérateur sur la voie des produits recyclables: ; Grâce aux quatre secteurs d'activité qui opèrent sur des marchés très différents, le savoir-faire et la compétence en matière de matières plastiques sont largement répandus dans l'entreprise.Un avantage qui a permis à K-TECH® de passer à la vitesse supérieure lors du développement de la première pièce automobile en matière recyclée post-consommation. Frank Schockemöhle : „En mars 2020, nous avons eu l'idée de développer un matériau PCR PP GF30. Et en décembre 2020, nous avons reçu les autorisations de production en série pour les générateurs de sons des supports.
Les exigences de sécurité et de qualité les plus élevées doivent être satisfaites.
L'utilisation de matières plastiques issues de déchets de consommation était alors un terrain inconnu pour la division Pöppelmann. Et pour cause : la construction automobile est soumise aux exigences les plus strictes en matière de sécurité et de qualité, et ce au même niveau dans le monde entier. Les propriétés requises pour les matériaux sont technologiquement complexes ; les pièces automobiles doivent résister à des charges élevées. Si l'on veut travailler dans ce secteur avec des matières recyclées, il faut pouvoir définir les propriétés des plastiques usagés de manière aussi précise et démontrable que pour les matières neuves.
Tout cela a été pris en compte dans la réflexion sur le composant qui pourrait convenir pour la première PCR chez K-TECH®. Finalement, le choix s'est porté sur le support pour les générateurs de sons, qui simulent le bruit des moteurs afin d'avertir à temps les cyclistes et les piétons de la présence de véhicules électriques presque silencieux. Le support est fixé à l'extérieur de la carrosserie. Cela a facilité l'entrée dans la tâche. En effet, les mesures concernant les odeurs ne sont pas aussi élevées à l'extérieur qu'à l'intérieur, explique Frank Schockemöhle.
Réussir le changement de matériel avec les fournisseurs et les clients
Des innovations de grande envergure comme celle-ci ne peuvent être réalisées qu'avec des partenaires tout au long de la chaîne d'approvisionnement. C'était également le cas dans ce cas : avant de proposer au client de changer de matériau, K-TECH® a développé et testé des recyclats post-consommation appropriés en collaboration avec un fournisseur.
Frank Schockemöhle regarde en arrière : „Chez K-TECH®, nous utilisons le matériel PIR depuis 2012 déjà et avons acquis une première expérience. Depuis, nous avons pu développer nos connaissances en matière de qualification des matériaux recyclés. Ces expériences ont ensuite été intégrées, avec celles de la production TEKU®, dans nos premières solutions PCR dans le secteur automobile. Nous avons également dû trouver comment traiter le matériau pour obtenir la qualité correspondante et le rendre à nouveau utilisable.
Ce n'est que lorsque les résultats de ces tests ont été convaincants que Frank Schockemöhle et son équipe, avec ses collègues commerciaux, ont présenté l'idée au client. „Nous avions avec nous les preuves correspondantes pour montrer que le passage du matériel neuf à la PCR fonctionne. Et c'est ainsi que nous avons vraiment réussi, en l'espace de neuf mois, à convertir une pièce de série existante de matériau vierge en matériau post-consommation.&ldquo ; Une vitesse record dans le secteur.
Dans le scope 3, l'économie circulaire est le levier le plus important
Et le développement se poursuit à un rythme effréné. La pression augmente. La nécessité de réduire les émissions de gaz à effet de serre pour au moins limiter les effets catastrophiques du changement climatique est scientifiquement prouvée. Les matériaux de production qui circulent en circuit fermé contribuent à la réduction des émissions de la catégorie Scope 3. Il s'agit des émissions indirectes d'une entreprise sur lesquelles elle n'a pas d'influence directe, car elles sont générées par les produits achetés &ndash ; comme par exemple les plastiques achetés à partir de produits neufs &ndash ; et en aval par l'élimination des produits vendus après utilisation.
Dans le scope 3, l'économie circulaire est le plus grand levier de réduction. En effet, de la même manière que ces émissions sont générées tout au long de la chaîne d'approvisionnement, c'est tout au long de cette chaîne qu'elles peuvent être réduites le plus efficacement. Un exemple : Lorsqu'une entreprise de plastique utilise des matières recyclées post-consommation dans sa production, cela a un effet positif aussi bien sur son propre bilan climatique que sur celui du client.
En même temps, le législateur fait avancer l'économie circulaire avec de nouveaux règlements et directives. Ainsi, la branche automobile a actuellement les yeux rivés sur Bruxelles : le Parlement européen et le Conseil européen y discutent d'un projet de la Commission européenne pour une mise à jour du règlement sur les véhicules hors d'usage (VHU). L'une des propositions prévoit que 25 % des plastiques utilisés dans les véhicules doivent provenir de produits recyclés post-consommation (PCR), dont au moins 25 % directement des véhicules hors d'usage.
La direction est prise. L'utilisation de PIR et de PCR va également gagner en importance dans la construction automobile au cours des prochaines années. Cela nécessite des développements dans la collecte et le tri des déchets, les procédés de recyclage et de traitement, les directives pour les cahiers des charges et les évaluations de la qualité. La mise en œuvre cohérente de la conception circulaire fait également partie des conditions du succès.
Nous n'attendons pas ce qui vient, mais nous allons vers l'économie circulaire. En collaboration avec nos clients et fournisseurs, nous cherchons et trouvons des projets phares qui montrent : L'utilisation de matériaux recyclés post-consommation dans la construction automobile est possible &ndash ; ici et maintenant. L'exemple le plus récent de la division K-TECH est la console de cric, qui répond d'ores et déjà à 100 % à la nouvelle version prévue de l'ordonnance sur les véhicules hors d'usage.
Frank Schockemöhle est confiant dans le fait que K-TECH® est sur la bonne voie : „Nous avons fermement implémenté l'ensemble du thème Design for Circularity dans le département de construction et de développement. Pour chaque nouveau projet, nous réfléchissons : Comment satisfaire les souhaits et les exigences du client avec les meilleures solutions pour la réduction des matériaux, l'économie circulaire et la protection du climat ? Si nous y parvenons, il sera beaucoup plus facile, dans les années à venir, de rassembler ces matériaux en grandes quantités et de les recycler pour en faire de bons plastiques. Nous pouvons ainsi proposer au client de bonnes solutions pour sa démarche de protection du climat. C'est ainsi que nous nous assurons aujourd'hui les matériaux de demain.“
Story
80% des nouveaux achats introduisent des recyclats post-consommation dans le circuit #éléments de protection #recycle
80% des nouveaux achats introduisent des recyclats post-consommation dans le circuit #éléments de protection #recycle
Que ce soit dans l'industrie automobile, la construction mécanique ou le secteur du bâtiment, les éléments de protection de la division KAPSTO® de Pöppelmann sont utilisés dans de nombreux secteurs industriels. ; Ils protègent les composants essentiels à la fonction et à la sécurité pendant la fabrication, le stockage et le transport. Fabriqués dans des matières plastiques de haute qualité, les articles KAPSTO® ne sont souvent utilisés que très peu de temps, parfois quelques minutes seulement. Ce fut le point de départ, en octobre 2022, de la plus grande extension de gamme jamais réalisée par KAPSTO®. Avec le passage progressif du programme standard de KAPSTO® à des éléments de protection fabriqués à partir de produits plastiques usagés recyclés, un matériau précieux reste désormais en circulation à long terme.
Thorsten Koldehoff, directeur mondial des ventes de KAPSTO®, se souvient : „Bien sûr, les objectifs de l'initiative stratégique de l'entreprise PÖPPELMANN blue® ont également enthousiasmé nos collègues. Qui ne voudrait pas contribuer à la protection du climat et à la préservation des ressources ? Pour les applications à courte durée de vie, il est inacceptable que le plastique de qualité ne soit utilisé qu'une seule fois.
Le nom de la division KAPSTO® de Pöppelmann est synonyme de „capuchons et bouchons&ldquo ; &ndash ; et il contient en même temps une partie de l'histoire de l'entreprise. En effet, c'est avec la fabrication d'un capuchon de poignée monté sur un bouchon en liège qu'a débuté en 1955 la branche plastique de l'entreprise, qui avait été fondée comme usine de liège.
Les éléments de protection de la gamme KAPSTO® semblent à première vue être des produits relativement simples. Mais c'est faux. En effet, dans de nombreux secteurs industriels, ils doivent aujourd'hui protéger de manière fiable des équipements très sensibles au cours de processus de production complexes. Les exigences en matière de qualité et de propriétés des matériaux sont élevées.
Qui réfléchit à la manière de fermer le cycle des matériaux doit savoir : Cela ne fonctionne qu'avec le recyclage des produits recyclés post-consommation (PCR). Les PCR sont fabriqués à partir de produits en plastique jetés après usage, par exemple les déchets d'emballages collectés dans la poubelle jaune. Une véritable économie circulaire signifie que les produits usagés deviennent de nouveaux produits, de qualité égale ou supérieure.
C'est un point auquel chacun devrait faire attention lorsqu'il lit des „recyclés&ldquo ;. Car il n'est pas rare qu'il s'agisse de recyclats post-industriels (PIR). Il s'agit de restes de production, c'est-à-dire de matériaux qui n'ont pas encore été utilisés. Bien entendu, le traitement des PIR contribue également à la préservation des ressources, car il réduit la consommation de matériaux neufs. Mais le PIR, tout comme les matériaux neufs, ne ferme le cycle des matériaux que lorsqu'il a été utilisé au moins une fois, éliminé puis recyclé. Car c'est l'idée de base de l'économie circulaire : les matériaux circulent dans le circuit pendant de nombreuses vies de produits et réduisent ainsi, par exemple dans le secteur des matières plastiques, la consommation de matières premières fossiles.
Et c'était précisément l'objectif déclaré de KAPSTO®, vers lequel les équipes impliquées se sont résolument dirigées depuis 2018 . „Le passage à la PCR a entraîné des tâches complexes, car les propriétés des matériaux varient&ldquo ; explique Holger Ommen, expert en PCR au sein du service commercial de KAPSTO®, en regardant en arrière. De nombreux tests et analyses ont été nécessaires pour répondre, par exemple, aux questions sur la résistance à la température. La production a également été confrontée à des défis lors du traitement de la PCR. Ainsi, les propriétés d'écoulement sont moins bonnes et les variations sont plus importantes par rapport au produit neuf.
Enfin, l'automne 2022 a vu le lancement de „la plus grande extension de programme jamais réalisée chez KAPSTO® ; comme le décrit le directeur des ventes Thorsten Koldehoff, le changement de matériel. „Après un travail de développement considérable, nous avons pu, à l'automne 2022, mettre à disposition 1900 articles en tant que variante en plastique durable.&ldquo ; Aujourd'hui, ce sont au total plus de 2000 articles qui peuvent être commandés à partir du programme standard KAPSTO® en tant que variante PCR.
Le résultat : la partie plastique des capsules et bouchons en plastique durable est composée à 100 % de PCR. Pour ce faire, KAPSTO® utilise le polyéthylène PCR (PCR-PE) et le polypropylène PCR (PCR-PP), deux matériaux recyclés. Tous les produits KAPSTO® en PCR-PE, PCR-PP et PCR-PE-HD portent le label écologique Ange bleu, qui est attribué aux produits respectueux de l'environnement et garantit que les produits sont composés d'au moins 80 % de recyclats post-consommation. A cela s'ajoutent, pour les couleurs spéciales, des articles en mélanges recyclés de PCR et de produits neufs („Blend"), dont l'impact CO2 est encore nettement inférieur à celui des variantes composées exclusivement de produits neufs.
La majorité des clients de KAPSTO® ont accueilli cette extension du programme avec enthousiasme, rapporte Holger Ommen. „Dans ce cas également, il s'est avéré que les solutions durables ne peuvent être mises en place avec succès qu'en commun. La flexibilité et l'ouverture au changement sont nécessaires de tous côtés, y compris chez les clients. Parfois, ce sont des habitudes, par exemple en ce qui concerne le choix des couleurs des articles, qui doivent être adaptées, parfois une nouvelle documentation sur les articles, tout à fait laborieuse, est nécessaire&ldquo ;, décrit-il un défi.
Mais KAPSTO® a convaincu &ndash ; et ce concrètement avec des chiffres, des données, des faits. En quelques clics, les acheteurs peuvent calculer, grâce au calculateur de CO2 en ligne sur le site web, la réduction des émissions de gaz à effet de serre en optant pour un élément de protection en matériau PCR plutôt que pour un produit neuf. Le client voit ainsi directement la valeur ajoutée de ces articles pour son propre bilan climatique&ldquo ; explique l'expert PCR de KAPSTO®. Il renvoie en outre aux envois d'échantillons que toute personne intéressée peut demander afin de tester les éléments de protection en recyclats post-consommation dans ses propres processus. „Cette offre est volontiers utilisée “.
Aujourd'hui, KAPSTO® livre environ 80% des nouvelles commandes pour lesquelles il existe une alternative de matériau dans son programme, dans la variante PCR. Un grand succès, également pour l'objectif d'économie circulaire en général. Mais le chemin est loin d'être terminé, souligne Holger Ommen. Dans la prochaine étape, nous voulons établir un système de reprise avec CapCylce&ldquo ; annonce-t-il. En collaboration avec les clients, nous coordonnons la reprise des éléments de protection usagés, à partir desquels nous fabriquons de nouveaux éléments de protection. La boucle est ainsi complètement bouclée. Nous avons déjà des entretiens avec des entreprises intéressées qui souhaitent retourner des quantités plus importantes.
Thorsten Koldehoff souligne qu'il existe de nombreuses bonnes raisons d'utiliser des éléments de protection adaptés à la circulation : „Aujourd'hui déjà, les OEM exigent l'utilisation de PCR. De plus, nous nous attendons dans un avenir proche à des législations européennes et nationales concernant les exigences en matière de taux de recyclage. Ces exigences seraient alors déjà satisfaites pour les produits concernés.
Story
L'HISTOIRE DU SUCCÈS PÖPPELMANN BLUE® #circulaire #recycle
L'HISTOIRE DU SUCCÈS PÖPPELMANN BLUE® #circulaire #recycle
Pöppelmann est l'un des pionniers de l'économie circulaire dans le domaine de la transformation des matières plastiques. Le moteur interne de cette évolution a été la création de l'initiative stratégique d'entreprise PÖPPELMANN blue® en 2018. Les associés, le conseil consultatif et la direction avaient alors décidé de lancer un premier projet pour un produit de série recyclable.
A peu près au même moment, des rapports sur des abus flagrants dans l'utilisation du plastique, comme la pollution des océans par le plastique, la présence de microparticules de plastique dans l'environnement et les voies douteuses d'élimination des déchets plastiques, ont attiré l'attention du public. Avec PÖPPELMANN blue®, l'entreprise a opposé à la critique justifiée sa propre conviction : Le plastique est le matériau de l'avenir &ndash ; si on le traite correctement.
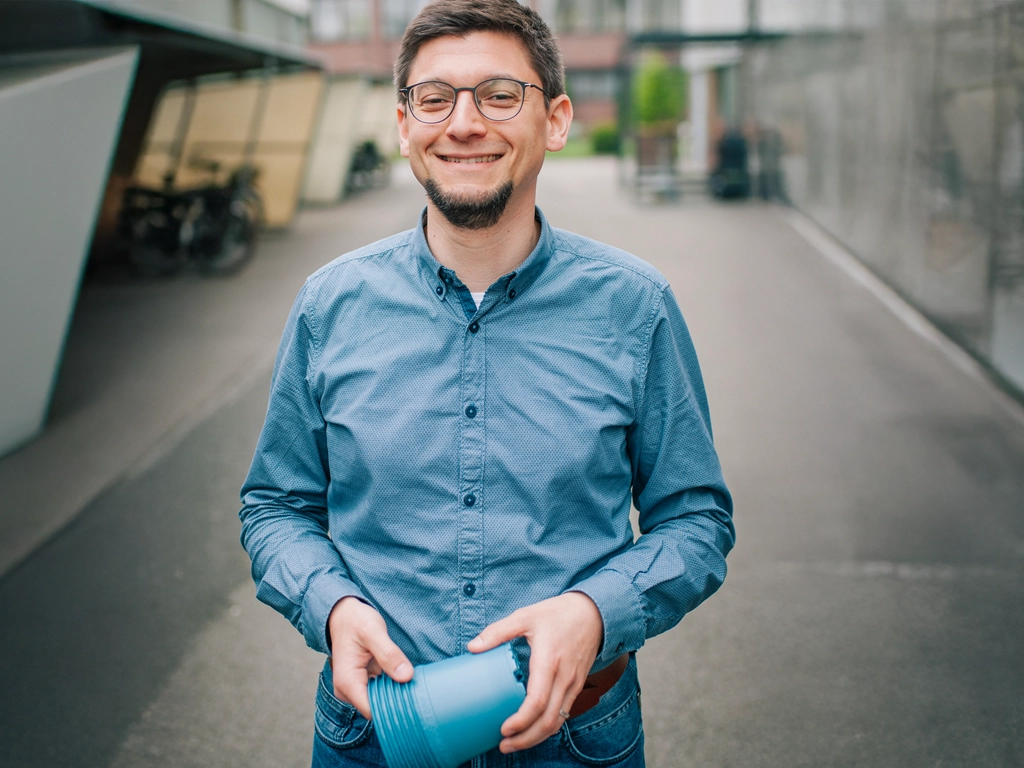
#circulaire
La stratégie et les objectifs de l'initiative sont développés au niveau le plus élevé de la direction de l'entreprise : Une fois par trimestre, le comité de pilotage PÖPPELMANN blue® se réunit avec des représentants des actionnaires, du conseil consultatif, de la direction ainsi que des experts techniques des divisions et des services centraux.
"Nous avons fait progresser très rapidement l'utilisation du recyclage dans les applications de série&ldquo ;.
L'interlocuteur central de l'initiative et le coordinateur des activités dans l'entreprise est Benjamin Kampmann. Il fait partie de l'équipe MORGEN en tant que „créateur de possibilités&ldquo ; spécialisé dans la préservation des ressources et la protection du climat. Dans l'interview, Benjamin a répondu à quelques questions sur PÖPPELMANN blue®.
Tout d'abord, comment peut-on associer le plastique à la durabilité ? En effet, le terme plastique éveille souvent des sentiments très négatifs. Pour beaucoup, notre matériau évoque d'abord la pollution des océans et de nombreux autres problèmes comme les microplastiques. Ne serait-il pas préférable qu'il n'y ait plus de plastique ?
C'est là que réside la question : ne vaudrait-il pas mieux que tel ou tel produit en plastique n'existe pas ? D'un point de vue écologique, renoncer est toujours la meilleure option. Mais de quoi voulons-nous ou pouvons-nous réellement nous passer ? Jetons un coup d'œil à notre portefeuille de produits chez Pöppelmann : KAPSTO® produit des éléments de protection qui sont indispensables dans la production industrielle et pour la protection des produits. Ou le domaine de la mobilité : nous voulons et devons être mobiles. Le plastique permet des solutions de construction légère pour les pièces automobiles produites par K-TECH®. Les produits alimentaires sont indispensables &ndash ; tout comme les emballages qui les protègent contre la détérioration et garantissent les normes d'hygiène. Les médicaments sont également essentiels. Ces deux secteurs concernent notre production chez FAMAC®. De même, nous avons besoin de produits pour l'horticulture, un marché que TEKU® approvisionne.
Si nous considérons que le renoncement total dans tous ces domaines n'est pas réaliste, il est clair qu'un monde sans ces produits est difficilement envisageable. La véritable question que nous devrions nous poser est donc celle de la Öcoefficacité.
Qu'est-ce que cela signifie?
La notion de Öcoefficacité décrit le rapport entre la création de valeur et les émissions et impacts environnementaux générés. L'objectif est de réaliser une solution de produit optimale en utilisant le moins possible de ressources et d'énergie. Cela implique également d'évaluer quel matériau permet d'atteindre au mieux cet objectif. C'est pourquoi nous considérons l'éco-conception comme la pierre angulaire du développement de nos produits. Cette approche de la conception va bien au-delà de la recyclabilité d'un emballage ou de l'utilisation de matériaux recyclés. Dans l'éco-conception, nous prenons en compte l'ensemble du cycle de vie d'un produit.
Comment peut-on, en tant que fabricant, exercer une influence sur l'ensemble de la vie d'un produit ?
En ne s'arrêtant pas à la porte de l'usine, mais en intégrant la logistique, l'utilisation et l'élimination. Cela ne vaut pas seulement pour les produits à courte durée de vie comme les emballages, mais aussi pour les composants à longue durée de vie, par exemple dans le secteur automobile.
Nous voulons toujours trouver la solution la plus fonctionnelle et la plus économique possible grâce à l'éco-conception. Il peut y avoir des conflits d'objectifs lorsque l'on réfléchit, par exemple, pendant la phase de développement, à ce qui est le plus important : une utilisation minimale de matériaux, qui peut être obtenue par une structure de matériaux non recyclables ? Ou la recyclabilité ?
Comment cette approche est-elle mise en œuvre dans l'entreprise ?
Au début de chaque développement de produit, nous nous demandons d'abord : quelle est la fonction principale du produit ? Et directement après : Comment pouvons-nous, avec notre solution, combiner rentabilité et durabilité écologique, c'est-à-dire un impact minimal sur l'environnement ? L'évaluation de l'impact environnemental est pour nous un critère important. L'empreinte carbone en fait partie, entre autres. Dans chaque développement de produit, construction et fabrication, nous mettons en avant les avantages de notre matériau. Nous réduisons ainsi pas à pas nos émissions de gaz à effet de serre et nous rapprochons de nos objectifs climatiques.
Cela nous amène maintenant à l'initiative PÖPPELMANN blue®, dans laquelle ces objectifs ont été définis. A-t-il été difficile de sensibiliser l'entreprise aux thèmes de la durabilité ?
La création de l'initiative n'a pas eu lieu dans le vide, mais sur la base d'une gestion environnementale déjà bien ancrée à l'époque. Depuis 1996, nous participons sur une base volontaire à l'Eco-Management and Audit Scheme&ldquo ; de l'Union européenne, en bref : EMAS. Ce système est considéré comme le plus exigeant au monde en matière de gestion environnementale durable. Sur cette base, nous avons introduit au fil des ans d'autres systèmes de gestion, par exemple la gestion de l'énergie. La protection de l'environnement et l'exigence d'une gestion durable et d'une utilisation parcimonieuse des matières premières de notre planète ont donc toujours figuré en tête de notre agenda.
Qu'est-ce qui a incité PÖPPELMANN blue® à accorder un tel poids dans ses objectifs stratégiques à l'économie circulaire et à la préservation des ressources, puis à la protection du climat à partir de 2022 ?
Lorsque nous avons créé PÖPPELMANN blue®, nous étions conscients des défis posés par la crise du plastique et, surtout, par la crise climatique. Nous voulions agir, car nous sommes convaincus que notre matériel et notre travail peuvent contribuer à de nouvelles solutions d'avenir. Dans ce contexte, le recyclage de notre précieuse matière première selon le modèle de l'économie circulaire est un aspect central. C'est dans ce contexte que la division TEKU® a décidé en 2017 de lancer un projet phare circulaire. Il s'agissait d'étudier comment fabriquer un pot de fleurs recyclable et comment utiliser des recyclats issus de déchets d'emballages, par exemple de la poubelle jaune, pour la fabrication de ce produit. Les premiers résultats du produit ont permis de développer le premier produit de série à partir de recyclats post-consommation : lors du salon IPM 2018, nous avons pu présenter notre pot de plantes bleu pour les plantes en pot. Ce phare a servi de point de départ à la création de l'initiative PÖPPELMANN blue®.
D'autres entreprises engagent souvent un(e) responsable du développement durable pour ces questions. Qui assume ce rôle chez Pöppelmann?
PÖPPELMANN blue® est ancré au plus haut niveau de gestion de l'entreprise. En effet, nous ne voulions pas isoler la durabilité dans un département. Chez nous, chacun et chacune est responsable de la durabilité dans son domaine. Chaque trimestre, des représentants des actionnaires, du conseil consultatif, de la direction et des experts des services centraux et des divisions se réunissent au sein du comité directeur de l'initiative. Ils se mettent d'accord sur de nouveaux projets et objectifs et les font avancer en permanence. Cette approche est l'une des recettes du succès, grâce à laquelle nous avons pu, par exemple, faire progresser très rapidement et très loin le thème de l'utilisation de matières recyclées dans les applications en série.
Comment l'initiative devient-elle visible et efficace dans le travail quotidien ?
La possibilité de contribuer par son propre travail à limiter le réchauffement de la planète motive et enthousiasme également au sein de l'entreprise. En même temps, il est très clair que nous devons nous imposer sur le marché avec nos produits et convaincre sur le plan économique. Lorsque nous parlons d'économie circulaire, de protection du climat et de préservation des ressources dans notre secteur, nous le faisons toujours en tenant compte de la rentabilité. C'est ainsi que s'est développée au fil du temps, dans les services et les équipes, une vision globale des exigences des clients. Nous disons aujourd'hui : chez nous, les aspects de durabilité sont assis à la table des décisions. Ici, elle est négociée sur un pied d'égalité avec des critères tels que la qualité, la rentabilité, la sécurité des processus et les avantages pour le consommateur.
Dans chaque division, il n'y a pas seulement des projets phares dans le cadre de PÖPPELMANN blue, mais aussi des applications en série qui ont mis le sujet sur la route et ont ainsi établi des normes dans toute la branche. Quelles étaient et quelles sont les conditions préalables à ce succès ?
Dans les projets phares, nous avons pu tirer de nombreux enseignements pour le développement d'autres produits circulaires. Pour citer un exemple : Dès le développement du produit, les exigences en matière de design doivent être remises en question. Ainsi, au tout début du projet, nous pouvons influencer l'utilisation de matières recyclées dans la production et la capacité de recyclage du produit. Pour les emballages en particulier, la conception pour le recyclage est devenue la norme, ou encore la conception pour la recyclabilité. En effet, les décisions prises à ce stade précoce contribuent déjà largement à garantir les flux de matériaux futurs.
Les clients suivent-ils cette voie?
De nombreux clients s'adressent désormais à nous de manière proactive, tandis que nous parvenons à convaincre d'autres clients de notre approche circulaire au cours de la phase de développement. Grâce à notre approche, nous remettons souvent en question les exigences initiales du produit. Dans la plupart des cas, nos propositions suscitent l'intérêt, par exemple en ce qui concerne la diversité des matériaux. Le traitement des matières recyclées exige de la flexibilité à différents niveaux. L'objectif n'est pas la productivité maximale, mais l'harmonisation de l'application, des processus et des matériaux pour un compromis optimal dans le sens de l'économie circulaire, de la durabilité et de la rentabilité.
Comment cette vision globale se répercute-t-elle sur les objectifs climatiques de Pöppelmann ?
Pour cela, je voudrais expliquer brièvement comment ces objectifs climatiques sont définis. Tout d'abord, nous avons déterminé notre empreinte carbone totale &ndash ; l'empreinte carbone de l'entreprise &ndash ; pour l'année 2021. Sur cette base, nous avons fixé nos objectifs climatiques pour 2030 selon la méthode basée sur la science de la Science Based Targets initiative (SBTi). Selon cette méthode, les émissions de gaz à effet de serre sont classées dans des catégories spécifiques, appelées „scopes&ldquo ;. Les scopes 1 et 2 mesurent les émissions qui se produisent directement chez nous, par exemple par la combustion d'essence, de diesel et de gaz et par la consommation d'énergie achetée. Les émissions du scope 3 sont générées indirectement tout au long de la chaîne d'approvisionnement, notamment par les marchandises achetées, les transports et l'élimination de nos produits, mais aussi, par exemple, par les déplacements domicile-travail de nos collaborateurs.
Et quels sont les objectifs climatiques que Pöppelmann s'est maintenant fixés?
Nous nous sommes engagés en 2023 auprès de la Science Based Targets initiative (SBTi) à réduire nos émissions absolues de portée 1 et 2 de 50% et nos émissions absolues de portée 3 de 25%, dans les deux cas jusqu'en 2030 par rapport à 2021. Nous sommes désormais tenus de recalculer et de publier les émissions de GES chaque année. ;. Nous publions les données les plus récentes dans notre rapport sur les gaz à effet de serre. Chacun de nos départements et divisions a formulé ses propres objectifs stratégiques pour contribuer à cet objectif climatique. Pour réduire les émissions de Sope 1 et de Scope 2, nous optimisons par exemple notre consommation d'énergie, nous achetons de l'électricité dans des parcs éoliens régionaux et nous construisons des installations photovoltaïques sur nos halls.
Et qu'en est-il des émissions du scope 3 ? Est-ce que l'économie circulaire entre en jeu ici?
Oui, c'est exactement ça. L'économie circulaire est pour nous le plus grand levier pour réduire les émissions de GES dans le scope 3. Comme nous l'avons décrit plus haut, nous n'avons qu'une influence indirecte sur ces émissions, car elles sont générées à l'extérieur de l'entreprise dans la chaîne d'approvisionnement. En effet, si ces émissions sont générées tout au long de la chaîne d'approvisionnement, c'est également tout au long de cette chaîne qu'elles peuvent être réduites le plus efficacement. Un exemple : Si une entreprise de plastique utilise des matières recyclées post-consommation au lieu de matières neuves dans sa production, cela a un impact positif sur son propre bilan climatique et sur celui de son client.
Qu'est-ce que cela signifie pour PÖPPELMANN blue®?
Comme je voulais le préciser, pour réaliser l'économie circulaire, il est indispensable d'avoir une vision globale des tâches. C'est pourquoi l'échange et le dialogue avec tous les acteurs de la chaîne de valeur sont essentiels. Nous voulons faire avancer activement les processus de transformation vers l'économie circulaire. Le lien avec la numérisation, par exemple par l'introduction du passeport produit numérique, peut générer à l'avenir de véritables plus-values pour l'organisation interne, la chaîne d'approvisionnement et la durabilité. Nous sommes en tout cas prêts à mettre nos connaissances et nos compétences en matière de plastique au service de cet objectif. Mais cela ne peut pas se faire seul, il faut travailler ensemble avec toutes les parties prenantes.