We have expanded our cleanroom capacities.
Plastic articles for the pharmaceutical industry and medical technology are subject to strict cleanliness and hygiene requirements in order to ensure maximum product protection and user safety. By investing in a clean room extension, we can now offer you even more options for manufacturing injection molded products in a low-particle environment. This includes, for example, large-format pharmaceutical packaging for the safe transportation of syringes made of glass and plastic.
Less particle sources, even more safety
From the injection molding cell to automated guided vehicles (AGVs) and automated packaging systems, the new cleanroom production generates less particle sources. This enables us to offer even greater product protection and the highest level of patient safety in the manufacture of plastic products for the pharmaceutical and medical technology industries.
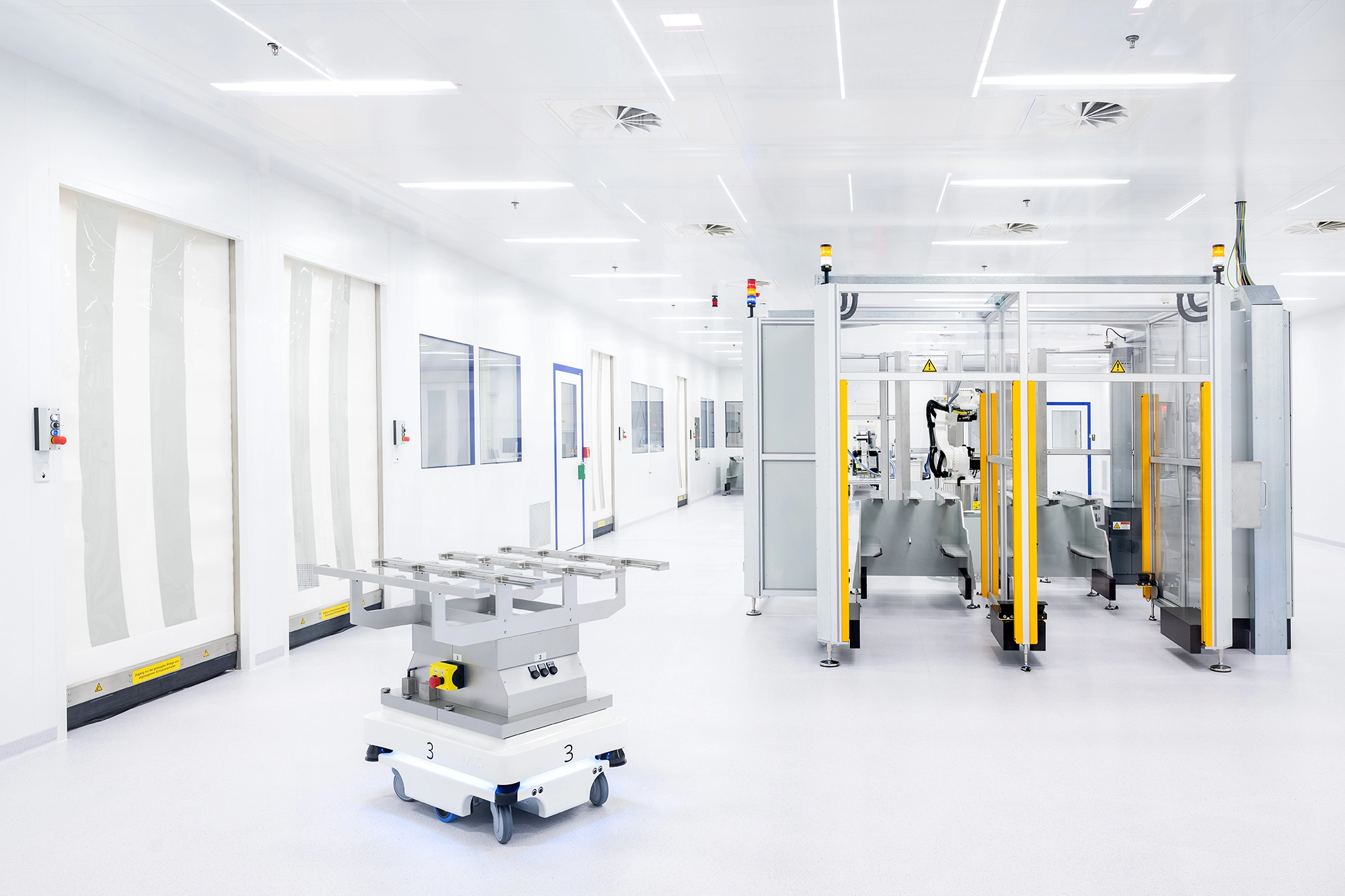
Expansion of the cleanroom capacities
The existing cleanroom of approx. 650 m2 is now being supplemented by a state-of-the-art and fully automated cleanroom of over 200 m2 with the injection molding machines located outside the cleanroom. The next expansion stage of the cleanroom for assembly and finishing processes is already being planned.
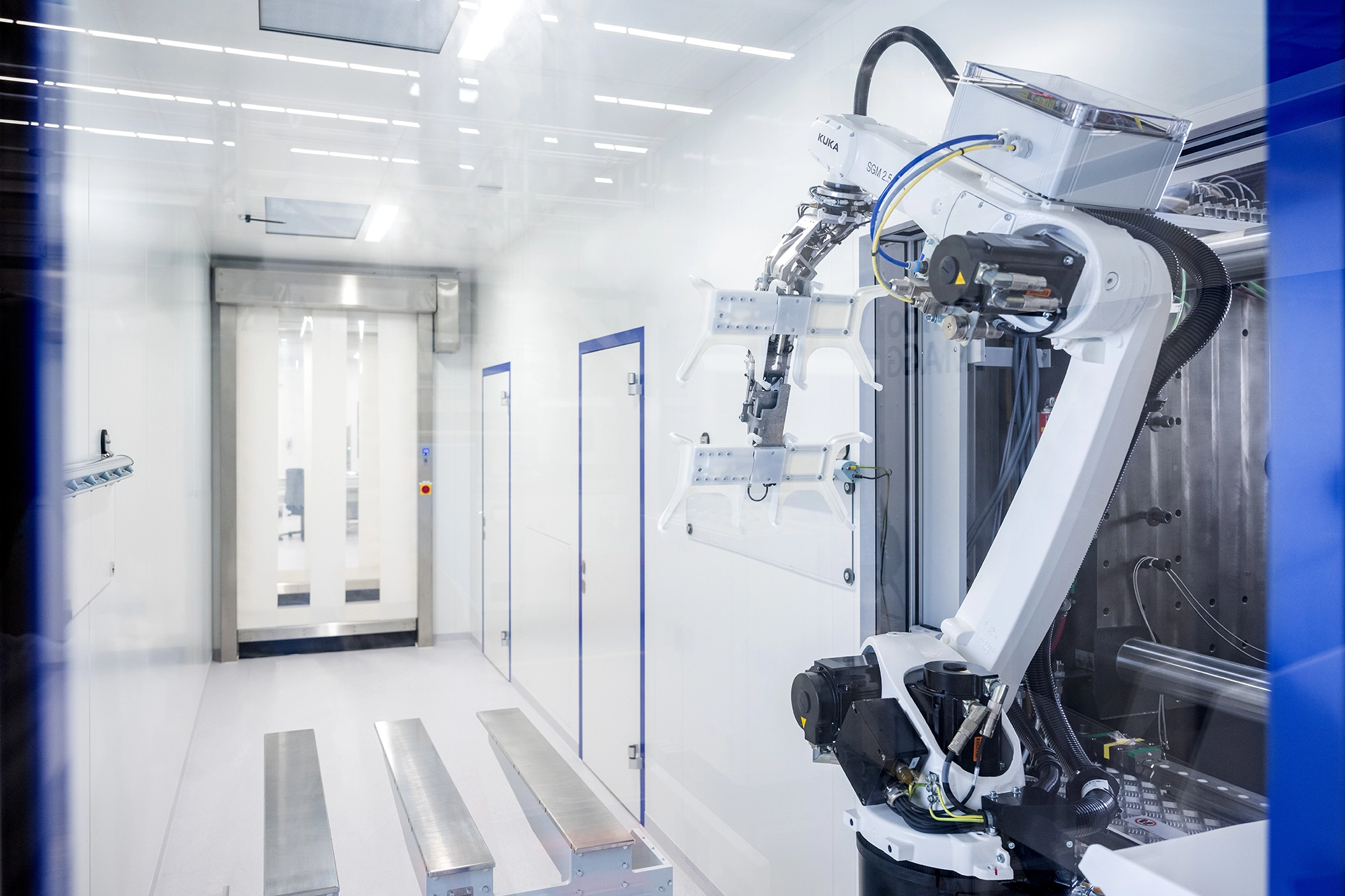
Seamless quality management, certified cleanliness
Our customers benefit from our many years of experience in the development and manufacture of plastic products with corresponding documentation according to the guidelines of GMP (Good Manufacturing Practice) - certified according to DIN EN ISO 13485. In four qualification steps, the manufacturing process is tested and documented in detail across all phases of industrialization.
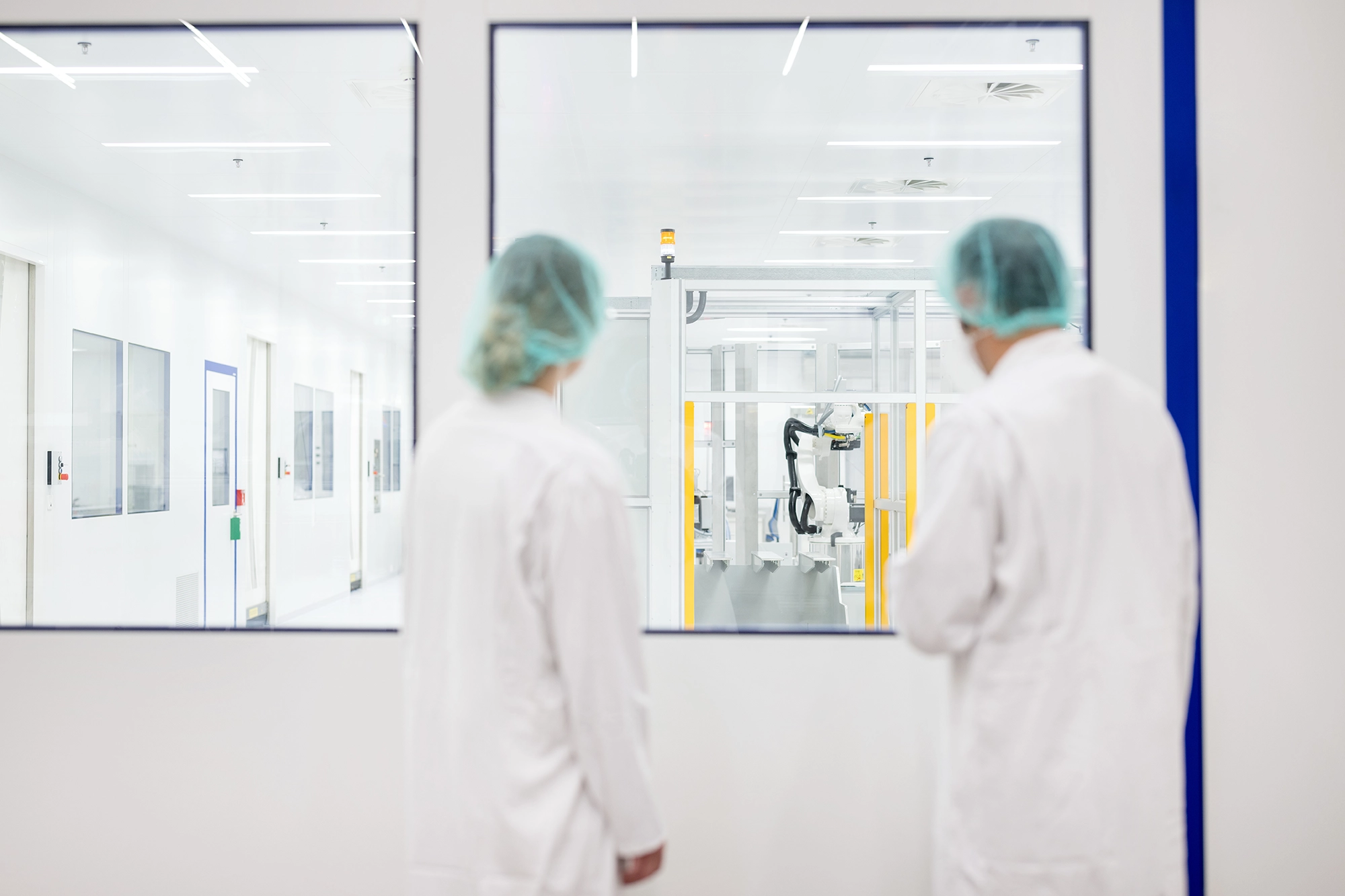
Reduction of greenhouse gas emissions
By installing the machines outside the cleanroom, we reduce the power requirement for the ventilation technology and keep the energy input per square meter of production area as low as possible. This has a correspondingly positive effect on the reduction of GHG emissions from these cleanroom products.

Awarded and
certified.
certified.
Highest quality combined with real climate protection.
A responsible use of natural resources to protect the environment and climate is a matter of course for many companies today. However, in areas such as medical technology and the pharmaceutical industry, maximum product protection, the highest level of patient safety and strict requirements for cleanliness and hygiene are the top priorities. The collaboration with our customers Drägerwerk AG & Co. KGaA and QIAGEN N.V. shows how sustainable and resource-saving plastic solutions can also be established in these strictly regulated areas.
think ahead
Together.
Together.
The responsible use of natural resources to protect the environment and the climate is a matter of course for many companies today. However, in areas such as medical technology and pharmaceuticals, regulatory requirements make it more difficult to implement. The focus is on application safety with maximum product protection. Nevertheless, we develop customized solutions that take into account the sustainable use of resources.
Material
We reduce the use of materials through resource-saving article concepts and efficient production processes.
Greenhouse gas emissions
The use of recycled materials, high recyclability and environmentally friendly production conditions can maximize GHG reductions.
Logistics &
process
By optimizing the design of the item, stacking and nesting can be improved - maximizing the quantity per package unit and minimizing setup time on the production floor.
Storage &
Energy
Optimized nesting allows for optimal use of existing capacity. The space required for internal and external logistics is reduced, resulting in cost savings.