Stories
Story
Black is out #plantpots #recycle
In January 2025, the color black was finally removed from the TEKU® standard range. A milestone. The entire product range is now fully recyclable: trays and pots, growing pallets and hanging baskets. Valuable material is preserved for many product lives. This is true circular economy – and reduces greenhouse gas emissions. Customers now benefit from a fully circular product range.
Sometimes a topic is in the air and a rather incidental idea suddenly becomes a game changer. TEKU® Division Manager Sven Hoping remembers: "It was 2017, in a small group meeting. At the time, the question suddenly came up: Wouldn't it be cool if the material for our plants came from the Yellow Bag?"
At that time, TEKU® already had more than forty years of experience in processing recyclates for the production of plant pots. However, until then it had almost exclusively been production waste. These so-called post-industrial recyclates (PIR) can be reused relatively easily in the production of new products, almost like new goods. This is because they are usually clean and sorted.
The situation is completely different with waste from plastic products that are disposed of after use, such as packaging. They end up in the Yellow Bag or Yellow Bin and have to be cleaned, sorted and analyzed in detail with regard to their material properties before being processed into post-consumer recyclate (PCR). However, in order to be able to use PCR without compromising on quality, technological expertise and a love of experimentation are required.
Pöppelmann's journey towards circular economy
That fits. Because innovative thinking paired with tenacity, pragmatism and competence is in the DNA of the material and process experts at Pöppelmann. This is evident barely a year later. In January 2018, TEKU® causes a stir at the leading international horticultural trade fair IPM. Blue plant pots, made from PCR and recyclable, are presented at the trade fair stand. The interest is huge.
With this trade fair appearance, Pöppelmann has set new standards for sustainable plastics processing and positioned itself as a pioneer of the circular economy in the industry. Also within the company: In the same year, the strategic corporate initiative PÖPPELMANN blue® is launched. This is where all the research is brought together to develop company-wide product concepts for the circular economy. The conclusion: plastic is far too valuable a material to be used only once.
But why are the doors blue, why is the company initiative called PÖPPELMANN blue®? The inspiration for this color and name came from the Ellen MacArthur Foundation's Circular Economy model. It distinguishes between two raw material cycles: the color green indicates the biological cycle of organic raw materials, the color blue the technical cycle of materials such as metal or plastic from production to recycling.
Blue is the new black
There is a second reason for the coloring of the pots. In the horticultural industry, black pots are considered the best and most favorable option for optimal plant growth. Opacity is a key factor here. The disadvantage: the near-infrared detectors in the sorting facilities of the dual systems cannot sufficiently detect black plastics. This is why black pots usually end up with the unsortable packaging waste and therefore end up in energy recovery after only one use.
This makes it clear: the use of recyclates is only the first step on the road to the circular economy. To close the loop, the product itself must also be recyclable. That is why the choice of color plays a major role. And this also presents the challenge of meeting all the conditions for optimum plant growth and process requirements in horticultural businesses, even with colorful pots.
Tight collaboration across departments to company-wide expertise has always been the answer to challenges like these at Pöppelmann, resulting in constant improvements in technology and production processes. In 2021, TEKU® introduces the resource-saving Circular360 category plants in a wide range of trendy colors, made from PCR and recyclable for disposal in the Yellow Bag, opaque and UV-resistant.
Without black consistently sustainable
By dispensing with black plastics in its standard range, TEKU® has now taken a decisive stand for climate protection and resource conservation. TEKU® Sales Manager Arno Zerhusen and Area Sales Manager Dirk Moormann are proud that this milestone has now been reached. "Our goal was and remains to meet our customers' high demands in terms of quality and efficiency and at the same time to achieve greater climate protection and resource conservation with our products", says Arno Zerhusen.
This is only possible with clean recycling streams. Dirk Moormann explains how TEKU® channels the right material into the production halls: "Suppliers are obliged to deliver pure and recyclable raw materials that do not introduce any non-recyclable components, such as black material, into the recycling process. Customers can be confident that our products are made from exactly these materials. Independent certifications such as the Blue Angel, cyclos-HTP and RecyClass guarantee compliance with strict environmental standards.“
Simon Lambrecht, Product Manager in Development TEKU®, points to the next steps: "We will not stop at this point. Together with our partners, we want to develop further material streams to keep valuable raw materials in the cycle." The circular economy can only be realized in cooperation with all players along the supply chain, he emphasizes. "We are dependent on partners who pursue the same goal. It does not work alone." One example: TEKU® is in close contact with suppliers in order to jointly find and test suitable materials and bring them into the cycle.
The added value of this commitment to climate protection and resource conservation can be measured in figures: The CO2 footprint of a recyclable PCR plant pot is reduced by 25 percent compared to a pot made from virgin material.
Division Head, Sven Hoping believes that the path taken in 2017 has been confirmed by both environmental and economic sustainability factors in the market. He says: "More and more companies in the large industry want to make their production processes more sustainable. This is where we come in and support professional horticulture with modern products that achieve optimum plant growth while protecting the environment and climate.“
Story
Economy and sustainability in harmony #packaging #5p
Economy and sustainability in harmony #packaging #5p
We are convinced that economic success and sustainability are not contradictory. Rather, we believe that combining these two aspects is the key to future-proof innovations that are both economically profitable and environmentally friendly.
An outstanding example of this is the redesign of a private label cup for dairy products, which our FAMAC® division developed in a joint project with the DMK Group.
The success of this project impressively demonstrates how intelligent adaptations to proven packaging solutions can save valuable resources. The material-reduced redesign of the container also impressed the board of the German Packaging Award 2024: DMK and Pöppelmann FAMAC® were recognized for this innovative project at the Fachpack trade fair in Nürnberg in the cost-effectiveness category.
Our holistic approach is based on five equally important questions. Read how we answered them in this packaging:
Are we effectively solving a real problem?
The revised container had to retain the existing functionality but be designed to be more resource-efficient. The result: by making structural adjustments to the design of the cup wall, the stability of the packaging is maintained even with reduced use of materials.
Does this solution pay off for us and our partners?
Less material usage not only means lower production costs, but also optimized logistics and therefore economic benefits for all parties involved, including a reduction in fees for the dual systems. The board of the German Packaging Award emphasized that 20 percent less plastic (polypropylene) is needed for production. In addition, 50 percent more cups now fit into a reusable transport box, which significantly increases efficiency in logistics. The reduced stacking distance also means that 50 percent more cups fit into the magazines of the filling systems, which has also increased the efficiency of the filling process.
Do we have a process that works quickly, efficiently and securely?
The adaptation of the injection molding process ensures that the sealing of the cup after filling runs smoothly despite the thinner wall thickness. This was achieved by inserting bars on the inside walls of the cup to compensate for the compression pressure. They are not visible to the consumer, but have a major impact: this reworking of the design saves more than 20 percent GHG emissions compared to typical market alternatives.
Does this solution convince all participants and stakeholders such as customers and consumers as well as interested associations?
The reduced use of materials does not have a negative impact on consumer use, but rather increases the attractiveness of sustainable packaging. The jury of the German Packaging Award praised the project as an exciting success story and particularly appreciated the partnership-based cooperation between DMK and Pöppelmann FAMAC®.
Is this solution eco-efficient?
By saving plastic, the new cup actively contributes to reducing CO2 emissions. DMK had already done away with the traditional steel lid for selected dairy products, thereby saving considerable amounts of plastic. The optimization of the injection-molded cup represents another important step towards conserving resources.
This example shows that sustainable product solutions are not only possible, but also economically viable. With hard work, meticulousness and a willingness to change, we develop solutions that convince the market and at the same time make a contribution to climate protection.
Story
Sustainability in medical technology:
New design reduces GHG emissions #pharma-medical #logistics
Sustainability in medical technology:
New design reduces GHG emissions #pharma-medical #logistics
Whoever is active in the field of medical technology must meet the highest requirements. After all, human lives are often at stake in this field. For example, with patients who need to be ventilated. Mike Landwehr, Deputy Sales Manager at FAMAC® Pharma-Medical, emphasizes: "Safety and performance are of course the top priority."
This means that it is not easy to quickly change a production process or replace a material. The use of recycled materials is also not possible in many cases. Nevertheless, FAMAC® Pharma-Medical is also facing up to the challenge of promoting the sustainable use of resources.
With success. This is shown by the example of the collaboration between FAMAC® Pharma-Medical and Drägerwerk AG & Co. KGaA for the development of housing parts for an HME breathing system filter. These filters minimize the risk of infection transmission by filtering viruses and bacteria during clinical ventilation and humidifying the patient's breathing air. They are used in anesthesia and intensive care medicine.
The FAMAC® team had to comply with various customer specifications when developing the airway filter housings. These included the square design instead of the previous round shape. Mike Landwehr: "We were able to combine this specification with further improvements. We convinced them with our suggestion of how to fit more parts into one package." Now the new variant enables space-saving stackability of the parts and thus significant optimizations in logistics, transport, storage and packaging. In addition, the square design means that there is less waste of filter material.
The concept of eco-design is the linchpin of the work of all development teams at Pöppelmann. This concept is characterized by a holistic view of the requirements – and by the willingness to approach tasks from different perspectives and to rethink. The environmental impact of a product is taken into account along its entire life cycle and kept as low as possible.
As in this case: the customer's specifications could be combined with further benefits - all of which contribute to reducing greenhouse gas emissions. This also includes the use of material residues that arise during the production process in plastics processing (waste). What used to end up as plastic waste is now melted down and reused.
So the new design of the housing part brings even more advantages today:
The production used means that 6 percent of GHG emissions can be reduced in relation to the annual production volume. In addition, the square design allows the parts to be stacked in a space-saving manner, thus significantly optimizing the logistics of packaging, storage and transport: where previously there was space for 4,800 parts loosely packed on a pallet, there are now 7,392 parts. This has enabled us to reduce GHG emissions in the area of logistics by 3.3 tons of CO2e – this corresponds to 32 percent; also in relation to the annual production volume
The redesign of the airway filters is not only convincing in terms of resource conservation: Drüger was awarded a Red Dot Design Award for the product, which has already been launched on the market. In the board's statement, it said: "In the sophisticated design of these respiratory protection filters, great importance was attached to the protection of patients and medical personnel."
More information on the Pöppelmann website:
Practical example of logistics optimization - Dräger
Story
Heading for the circular economy in top gear #automotive #recycle
Heading for the circular economy in top gear #automotive #recycle
The path to a genuine circular economy is one of the key strategic challenges in the automotive industry. For a long time, it was considered technically unfeasible to use post-consumer recyclates in car manufacturing. But we have done it! And we are ready to implement the EU's planned legal requirements for the use of recyclates in car manufacturing (End of Life Vehicles Directive) together with our customers.
Frank Schockemöhle, Head of Technology Management at Pöppelmann, still remembers a conference in June 2022: "I was invited to give an insight into our work on the use of recycled materials in automotive construction. The previous speaker concluded his presentation with the words: 'It will be another ten years before post-consumer material is in cars.' Then I took the microphone and was able to say: Thank you very much. My theme is that we are already in series production.“
Because the Pöppelmann division K-TECH® had already been involved in the design and development of automotive components for the circular economy for a long time at that time. The strategic sustainability initiative PÖPPELMANN blue® was launched in 2018. From then on, the topics of circular economy and resource conservation set the direction throughout the company. Conclusion: "Plastic is far too valuable a material to be used only once."
From now on, post-consumer recyclates (PCR) were the focus of interest: plastics made from products disposed of after use, such as recycled waste from the yellow bag. Even before PÖPPELMANN blue® was launched, TEKU® had been producing pots from post-industrial recyclates (PIR), i.e. production waste, for more than 50 years. This expertise was the starting point for the gradual conversion of TEKU® production to post-consumer recyclates after the company initiative was founded.
This is how a special Pöppelmann effect acts as an accelerator on the way to recyclable products: Thanks to the four business divisions, which operate in very different markets, know-how and expertise in plastics are broadly diversified within the company. An advantage that enabled K-TECH® to shift into top gear when developing the first car component made from post-consumer recyclate. Frank Schockemöhle: "In March 2020, we had the idea for the material development of a PCR PP GF30. And in December 2020, we received the series approval for the sound holder generators."
The highest safety and quality requirements must be met
The use of plastics from consumer waste was uncharted territory in the Pöppelmann division at the time. For good reason: the highest safety and quality standards apply in automotive engineering, and at the same level worldwide. The required material properties are technologically complex; car components have to withstand high loads. Anyone who wants to work with recyclates in this industry must be able to define the properties of used plastics just as precisely and verifiably as for new materials.
All this was taken into account when considering which component might be suitable for the PCR premiere at K-TECH®. In the end, the choice fell on the holder for sound generators, which simulate engine noise to warn cyclists and pedestrians in good time of the almost silent electric vehicles. The holder is attached to the outside of the vehicle body. This made it easier to get started with the task. "Because in the exterior area, the odor levels are not as high as in the interior“, explains Frank Schockemöhle.
Material changeover succeeds together with suppliers and customers
Far-reaching innovations like this can only be implemented with partners along the entire supply chain. This also applied in this case: before the material changeover was proposed to the customer, K-TECH® worked with a supplier to develop and test suitable post-consumer recyclates.
Frank Schockemöhle looks back: "We have been processing PIR material at K-TECH® since 2012 and have gained initial experience. Since then, we have been able to continuously expand our knowledge of the qualification of recyclates. This experience, together with the experience gained from TEKU® production, then flowed into our first PCR solutions in the automotive sector. We also had to find out how we could process the material in order to achieve the right quality and make it reprocessable."
Only when the results of these tests were convincing did Frank Schockemöhle and his team, together with their sales colleagues, present the idea to the customer. "We had the relevant evidence with us to show that the material conversion from virgin material to PCR works. And so we actually managed to convert an existing series component from virgin material to post-consumer material within nine months." A record speed in the industry.
In Scope 3, the circular economy is the biggest lever
And the development continues. The pressure is increasing. The need to reduce greenhouse gas emissions in order to at least limit the catastrophic effects of climate change is scientifically proven. Production material that circulates in a loop contributes to the reduction of Scope 3 emissions. These are the indirect emissions of a company over which it has no direct influence, as they are caused by purchased products - such as purchased plastics from virgin materials - and subsequently by the disposal of the products sold after use.
In Scope 3, the circular economy is the biggest lever for reduction. This is because just as these emissions are generated along the entire supply chain, they can also be reduced most effectively along the entire supply chain. One example: If a plastics company uses post-consumer recyclates in production, this has a positive impact on both its own carbon footprint and that of the customer.
At the same time, legislators are driving the circular economy forward with new regulations and directives. The automotive industry is currently looking to Brussels, where the EU Parliament and European Council are discussing a draft from the EU Commission for an update to the End-of-Life Vehicles Regulation (ELV). One of the proposals in it stipulates that 25% of the plastics used in vehicles must come from post-consumer recyclates (PCR) and at least 25% of this must come directly from end-of-life vehicles.
The direction is set. The use of PIR and PCR will also become increasingly important in automotive engineering in the coming years. This requires further developments in waste collection and sorting, recycling and processing methods, specifications and quality assessments. The consistent implementation of circular design is also one of the prerequisites for success.
We are not waiting to see what comes next, we are moving towards the circular economy. Together with our customers and suppliers, we are looking for and finding lighthouse projects that demonstrate the use of post-consumer recyclates in automotive manufacturing is possible - here and now. The most recent example from the K-TECH® division is the attachment bracket for car jacks, which is already 100% compliant with the planned new version of the End-of-Life Vehicle Ordinance.
Frank Schockemöhle is confident that K-TECH® is on the right track: "We have firmly implemented the entire topic of 'Design for Circularity' in the design and development department. With every new project we consider: How do we fulfill the customer's wishes and requirements with the best solutions for material reduction, circular economy and climate protection?" Looking ahead, he says: "An important topic for the future will be the reduction of material diversity. If we succeed in this, it will be much easier in the next few years to combine these materials into larger volumes and recycle them again to make good plastics. In this way, we can show our customers good solutions for their path towards climate protection. This is how we secure the materials of tomorrow today."
Story
80% of new orders bring post-consumer recyclates into the cycle #protective elements #recycle
80% of new orders bring post-consumer recyclates into the cycle #protective elements #recycle
Whether in the automotive industry, mechanical engineering or the construction sector: the protective elements from Pöppelmann's KAPSTO® division are used in many industrial sectors.T hey protect function-critical and safety-relevant components during production, storage and transport. Made from high-quality plastics, KAPSTO® items are often only used for a very short time, some for just a few minutes. In October 2022, this was the starting point for the largest program expansion ever at KAPSTO®. With the gradual conversion of the KAPSTO® standard program to protective elements made from recycled used plastic products, valuable material now remains in the cycle in the long term.
Thorsten Koldehoff, Global KAPSTO® Sales Manager, recalls: "Of course, the goals of the strategic corporate initiative PÖPPELMANN blue® also inspired our colleagues. Who wouldn't want to contribute to climate protection and resource conservation? For short-lived applications in particular, it is unacceptable that high-quality plastic is only used once.
The name of the Pöppelmann division KAPSTO® stands for "caps and stoppers" – and it also contains a piece of company history. The plastic era of the company, which was founded as a cork factory, began in 1955 with the production of a handle cap that was placed on a cork.
At first glance, protective elements from the KAPSTO® portfolio appear to be relatively simple products. But that is wrong. After all, they have to reliably protect highly sensitive technology during complex production processes in many industrial sectors today. The demands on quality and material properties are high.
If you are thinking about how material loops can be closed, you need to know: This only works with the recycling of post-consumer recyclates (PCR). PCR is made from plastic products that have been disposed of after use, for example from packaging waste collected in the yellow garbage can. A genuine circular economy means that used products are turned back into new products of the same or higher quality.
This is something everyone should be aware of when reading about "recyclates". This is because it is not uncommon for post-industrial recyclates (PIR) to be meant. These are leftovers from production, i.e. material that has not yet been used. Of course, the processing of PIR also helps to conserve resources because it reduces the consumption of virgin material. However, just like new goods, PIR only closes the material cycle once it has been used at least once, disposed of and then recycled. After all, this is the basic idea behind the circular economy: materials circulate for many product lives in the cycle and thus reduce the consumption of fossil raw materials.
And this was precisely the declared goal of KAPSTO®, which the teams involved have been consistently pursuing since 2018 . "The switch to PCR involved complex tasks, as the material properties vary," explains Holger Ommen, PCR expert in KAPSTO® sales, looking back. "We had to go through a number of learning processes before we were successful." Extensive tests and analyses were necessary to clarify issues such as temperature resistance. There were also challenges for production when processing PCR. For example, the flow properties are poorer and their fluctuations greater compared to virgin material.
Finally, the largest program expansion ever at KAPSTO® was launched in autumn 2022, as Sales Manager Thorsten Koldehoff describes the material change. "After extensive development work, we were initially able to make 1900 items available as a variant made of sustainable plastic as standard in autumn 2022." Today, a total of more than 2000 items from the standard KAPSTO® range can be ordered as a PCR variant.
The result: The plastic content of the sustainable plastic caps and plastic stoppers consists of 100% PCR. KAPSTO® uses the recycled material PCR polyethylene (PCR-PE) and PCR polypropylene (PCR-PP). All KAPSTO® products made from PCR-PE, PCR-PP and PCR-PE-HD bear the Blue Angel eco-label, which is awarded for environmentally friendly products and guarantees that the products are made from at least 80% post-consumer recyclates. In addition, there are articles in recycled mixtures of PCR and virgin material ("Blend") for special color requests, which still have a significantly lower CO2 impact compared to variants made exclusively from virgin material.
The majority of KAPSTO® customers have responded enthusiastically to this program extension, reports Holger Ommen. "In this case, too, it has been confirmed that sustainable solutions can only be successfully implemented together. Flexibility and openness to change are necessary on all sides, including with customers. Sometimes it is habits, for example in the color selection of articles, that have to be readjusted, sometimes it is necessary to create new article documentation," he describes one challenge.
However, KAPSTO® convinced – with concrete figures, data and facts. With just a few clicks, buyers can use the online CO2 calculator on the website to find out how greenhouse gas emissions are reduced if they opt for a protective element made of PCR material instead of virgin material. "This also allows the customer to see directly what added value these items offer for their own carbon footprint", explains the KAPSTO® PCR expert. He also refers to the sample shipments that anyone interested can request in order to test the protective elements made from post-consumer recyclate in their own processes. "This offer is gladly used."
KAPSTO® now delivers around 80% of new orders for which there is a corresponding material alternative in the range in the PCR variant. A great success, also for the goal of a circular economy as a whole. But the journey is far from over at this point, emphasizes Holger Ommen. "In the next step, we want to establish a recycling system with CapCycle," he announces. "Together with the customer, we coordinate the recycling of used protective elements, from whose material we manufacture new protective elements. This closes the cycle completely. We are already in talks with interested companies that would like to return larger quantities."
Thorsten Koldehoff emphasizes that there are many good reasons for using circular protective elements: "OEMs are already demanding the use of PCR. In addition, we expect EU and national legislation regarding recycling quota requirements in the near future. These requirements would then already be met for the products in question."
Story
The SUCCESS STORY PÖPPELMANN BLUE® #circular #recycle
The SUCCESS STORY PÖPPELMANN BLUE® #circular #recycle
Pöppelmann is one of the pioneers of the circular economy in the field of plastics processing. The internal driving force behind this development was the founding of the strategic corporate initiative PÖPPELMANN blue® in 2018, when the shareholders, advisory board and management decided to launch an initial project for a circular series product.
Around the same time, reports about blatant misuse of plastic, such as plastic pollution of the world's oceans, microplastic particles in the environment and questionable disposal methods for plastic waste, began to hit the headlines. With PÖPPELMANN blue®, the company countered the justified criticism with its own conviction: Plastic is the material of the future, if it is handled correctly.
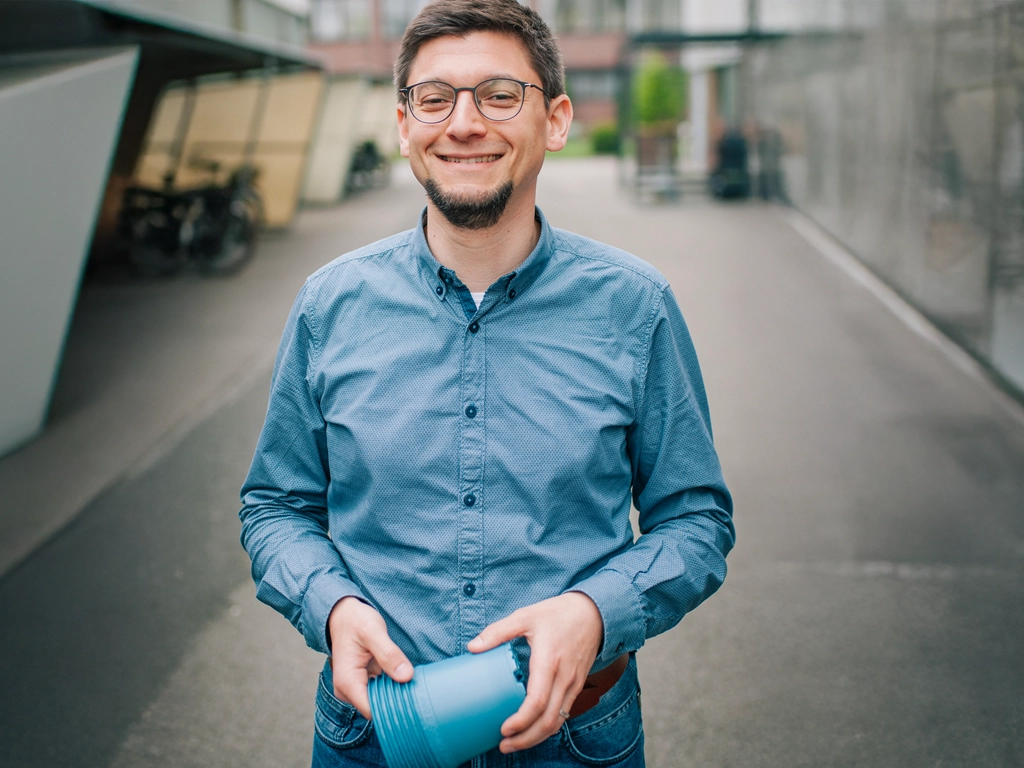
#circular
The strategy and objectives of the initiative are developed at the highest management level of the company: Once a quarter, the PÖPPELMANN blue® steering committee meets with representatives of the shareholders, advisory board, management and technical experts from the divisions and central departments.
"We have made very rapid progress in the use of recyclates in series applications“.
The central contact person for the initiative and coordinator of activities within the company is Benjamin Kampmann. He is part of the TOMORROW team as a "creator" with a focus on resource conservation and climate protection. In this interview, Benjamin answers some questions about PÖPPELMANN blue®.
First of all, the question of how plastic can be associated with sustainability at all. After all, the term plastic often evokes very negative feelings. Many people first think of our material in terms of the pollution of the oceans and many other problems such as microplastics. Wouldn't it be best if there were no more plastic?
This begs the question: Wouldn't it be better if this or that plastic product didn't exist at all? From an environmental point of view, doing without is always the best option. But what are we really willing or able to do without? Let's take a look at our product portfolio at Pöppelmann: KAPSTO® produces protective elements that are indispensable in industrial production and as product protection. Or the area of mobility: We want and need to be mobile. Plastics enable lightweight construction solutions for vehicle parts that K-TECH® produces. Food is indispensable - and so is the packaging that protects it from spoilage and ensures hygienic standards. Medicines are also essential. Both sectors affect our production at FAMAC®. We also need products for horticulture, a market that TEKU® supplies.
If we consider complete abandonment in all these areas to be unrealistic, it becomes clear that a world without these products is hardly conceivable. The real question we should be asking ourselves is therefore one of eco-efficiency.
What does that mean?
The term "eco-efficiency" describes the relationship between value creation and the emissions and environmental impact caused. The aim is to achieve the best possible product solution with the least possible use of resources and energy. This also includes evaluating which material is best suited to achieving this goal. This is why, for us, requirements-oriented eco-design is the turningpoint of product development. This design approach involves much more than the recyclability of packaging or the use of recycled materials. In eco-design, we look at the entire life cycle of a product.
How can manufacturers influence the entire product life cycle?
By thinking beyond the factory gate to include logistics, use and disposal. This applies not only to short-lived products such as packaging, but also to long-lasting components, for example in the automotive sector.
We always want to find the most functional and economical solution possible through eco-design. This can lead to conflicting goals, for example when you think about what is more important during the development phase: minimizing the use of materials, which can perhaps be achieved by using a non-recyclable material structure? Or recyclability?
How is this approach implemented in the company?
At the beginning of every product development, we first ask ourselves: What is the core function of the product? And immediately afterwards: How can we combine cost-effectiveness and environmental sustainability, i.e. minimizing environmental impact, with our solution? The evaluation of the environmental impact is an important criterion for us. This includes, among other things, the CO₂ footprint. We work to maximize the advantages of our material in every product development, design and production process. In this way, we are reducing our greenhouse gas emissions step by step and moving closer to our climate targets.
This brings us to the PÖPPELMANN blue initiative, in which these targets were defined. Was it difficult to raise awareness of sustainability issues within the company?
The initiative was not founded in a vacuum, but on the basis of an environmental management system that was already firmly established at the time. Since 1996, we have been voluntarily participating in the European Union's Eco-Management and Audit Scheme (EMAS). It is considered the most demanding system for sustainable environmental management worldwide. Building on this, we have introduced further management systems over the years, such as energy management. The topic of environmental protection and the aspiration to operate sustainably and use the earth's raw materials sparingly have therefore always been at the top of our agenda.
What was the impetus for PÖPPELMANN blue to give such weight to the circular economy and resource conservation and, from 2022, to climate protection in its strategic goals?
When we founded PÖPPELMANN blue®, we were aware of the challenges posed by the plastic crisis and, above all, the climate crisis. We wanted to take action because we are convinced that we can contribute to new, future-proof solutions with our material and our work. The recycling of our valuable raw material according to the circular economy model is a key aspect of this. With this in mind, the TEKU® division decided to launch a circular lighthouse project in 2017. The aim was to investigate how a recyclable plant pot can be manufactured and how recyclates from packaging waste, for example from the yellow garbage can, can be used to produce this product. The initial product results led to the first series product made from post-consumer recyclate: we presented our blue plant pot for herbs at IPM 2018. This lighthouse became the initial spark for the founding of the PÖPPELMANN blue® initiative.
Other companies often hire a sustainability manager for these topics. Who takes on this role at Pöppelmann?
PÖPPELMANN blue® is anchored at the highest management level of the company. We did not want to isolate sustainability in one department. Instead, everyone in our company is a sustainability manager in their own area. In the initiative's steering committee, representatives of the shareholders, the advisory board, the management and experts from the central departments and divisions exchange ideas on a quarterly basis. They constantly agree on new projects and goals and continuously drive them forward. This approach is one of the recipes for success, which has enabled us, for example, to make very rapid progress with the use of recycled materials in series applications.
How does the initiative become visible and effective in everyday working life?
The opportunity to contribute to limiting global warming with your own work motivates and inspires people within the company. At the same time, it is very clear that we have to survive on the market with our products and be economically convincing. When we talk about the circular economy, climate protection and resource conservation in our industry, we always do so under the premise of economic efficiency. Over time, our departments and teams have developed a holistic view of our customers' requirements. Today, we say that sustainability aspects are part of our decision-making process. Here, it is negotiated on an equal footing with criteria such as quality, cost-effectiveness, process reliability and consumer benefits.
In the meantime, there are not only lighthouse projects in each division as part of PÖPPELMANN blue®, but also series applications that have brought the topic to the streets and set standards across the industry. What were and what are the prerequisites for this success?
In the lighthouse projects, we were able to gain many insights for the development of further closed-loop products. To name one example: Design requirements need to be scrutinized as early as the product development stage. In this way, we can influence the use of recyclates in production and the recyclability of the product at the very beginning of the project. Design for recycling, or design for circularity, has now become the standard for packaging in particular. Even the decisions made at this early stage make a significant contribution to securing future material flows.
Are customers going down this path?
Many customers now approach us proactively, while we are able to convince other customers of our circular approach during the development phase. Our approach means that we often question original product requirements. In most cases, our proposals are met with interest, for example when it comes to material diversity. The processing of recyclates requires flexibility in various areas. The objective here is not maximum productivity, but rather the coordination of application, processes and material for an optimal compromise in terms of the circular economy, sustainability and cost-effectiveness.
How does this holistic view affect Pöppelmann's climate targets?
I would like to briefly explain how these climate targets are defined. First of all, we determined our complete CO2 footprint - the corporate carbon footprint - for 2021. On this basis, we set our climate targets for 2030 using the science-based method of the Science Based Targets initiative (SBTi). According to this method, greenhouse gas emissions are divided into certain categories, namely "scopes". Scope 1 and Scope 2 measure the emissions that arise directly on site, for example through the combustion of petrol, diesel and gas and through the consumption of purchased energy. Scope 3 emissions are generated indirectly along the supply chain, including through purchased goods, transportation and disposal of our products, but also through employee commuting, for example.
And what climate targets has Pöppelmann now set itself?
We have made a commitment to the Science Based Targets initiative (SBTi) in 2023 to reduce our absolute Scope 1 and 2 emissions by 50% and our absolute Scope 3 emissions by 25%, in each case by 2030 compared to 2021. We are now obliged to recalculate and publish GHG emissions every year. We publish the latest data in our greenhouse gas report. Each of our departments and divisions has formulated its own strategic goals to contribute to this climate target. To reduce Scope 1 and Scope 2 emissions, for example, we are optimizing our energy consumption, procuring electricity from regional wind farms and building solar power systems on our buildings.
And what about the emissions in Scope 3? Does the circular economy come into play here?
Yes, that's exactly it. For us, the circular economy is the biggest lever for reducing GHG emissions in Scope 3. As described above, we only have an indirect influence on these emissions, as they are generated in the supply chain outside the company. Just as these emissions are generated along the entire supply chain, they can also be reduced most effectively along the entire supply chain. One example: If a plastics company uses post-consumer recyclates instead of virgin material in production, this has a positive impact on both its own carbon footprint and that of the customer.
What does this mean for PÖPPELMANN blue®?
As I wanted to make clear, a holistic view of the tasks is essential for achieving a circular economy. That is why exchange and dialog with all players in the value chain is of fundamental importance. We want to actively drive forward the transformation processes towards a circular economy. The link with digitalization, for example through the introduction of the Digital Product Passport, can generate real added value for the internal organization, the supply chain and sustainability in the future. We are certainly prepared to contribute our knowledge and expertise in dealing with plastics to this goal. However, this cannot be achieved alone, but only together with all those involved.