New hall sets new standards
We have achieved a milestone in our company history: In our Plant 2 in Brockdorf / Lohne (Oldenburg), we celebrated the opening of one of the most modern production facilities in the plastics industry in Europe. Almost exactly two years after the groundbreaking, we celebrated with project stakeholders and all employees of the KAPSTO® division the relocation of the business unit to the new Hall 43. “In times when many industrial companies are turning their backs on Germany and building new facilities abroad, we have made a clear commitment to the production site in Lohne with this facility,” explained Vincent Otto, grandson of the company founder Josef Pöppelmann, on behalf of the owning family. “As a family, we feel connected to the region and the people here,” he affirmed during a celebratory event in his words of thanks to the planning offices, tradespeople, the Pöppelmann construction team, and all project participants.
Cutting-edge technology, greater flexibility, more climate protection
The new hall, with approximately 16,500 square meters of floor space and 23,400 square meters of gross floor area, is the new home for the KAPSTO® business unit and Pöppelmann’s small parts production. “With cutting-edge technology, energy-efficient production processes, and digitalization, we are not only creating additional capacities but also setting new standards in flexibility and customer service,” emphasizes Thorsten Koldehoff, Global KAPSTO Sales Director. For the first time, all company processes are interconnected under one roof—from material supply and production to further processing and logistics—while maintaining maximum sustainability and the most modern working conditions. In January 2025, the relocation of production from Plant 1 began. In the coming months, final details will be completed. Then KAPSTO will produce here under cleanroom conditions.
New building with a concept
The goal of the construction concept was to achieve a new level of flexibility, speed, and sustainability by efficiently designing production conditions, the work environment, and communication pathways. In his speech, Managing Director Norbert Nobbe explained the approach: “We consistently did not think about the building first but developed optimal processes and then built the hall around them.” This approach has made it possible to realize a state-of-the-art small parts manufacturing facility for injection-molded parts. The largest Pöppelmann hall to date allows for further development and also sets standards in terms of sustainability, Nobbe emphasized.
In the realization, the company adhered to the guidelines of the German Sustainable Building Council (DGNB), after which the hall will also be certified. Pöppelmann already achieved the highest certification level “Platinum” for this construction project in the DGNB pre-certification. The evaluation includes, among other things, the 2000 kWp photovoltaic system on the roof and southern façade, the intelligent use of energy flows, the green roof covering an area of nearly 10,500 square meters, the use of a 650 cubic meter rainwater storage system to conserve drinking water, and particularly the materials used in construction.
Photo:
Circular-capable KAPSTO parts as a guideline for the production of the future: from left Jan Römann (Production Manager KAPSTO), Christian Schwarck (Managing Director), Torsten Mairose (Head of Pöppelmann Construction Team), Felicitas Pöppelmann (Pöppelmann Family), Norbert Nobbe (Managing Director), Jakoba Lesemann (Pöppelmann Family), Felix Forst (Pöppelmann Family), Thorsten Koldehoff (Global Sales Director KAPSTO), Maximilian Forst (Pöppelmann Family), Vincent Otto (Pöppelmann Family), Christoph Tölle (Works Council Chairman), and Matthias Lesch (Managing Director).
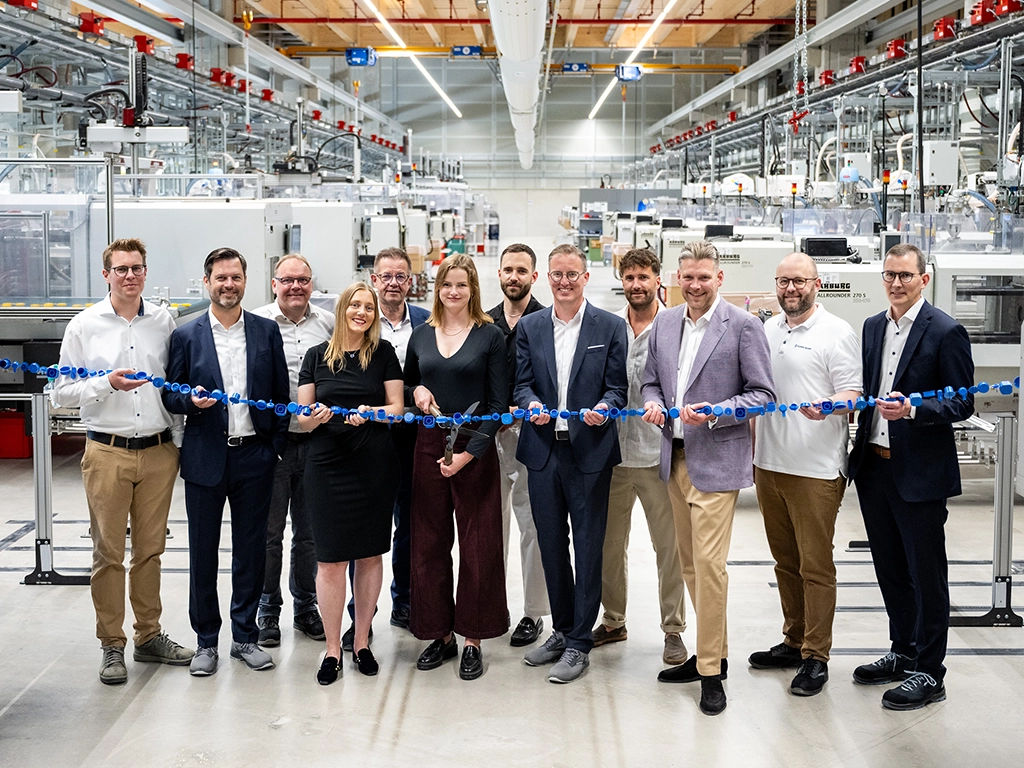