New Level in Clean Room Production
With the commissioning of a fully automated packaging system, Pöppelmann FAMAC® offers new opportunities for the production of plastic products that meet the strict requirements of the pharmaceutical and medical technology industries.
More Space, Higher Capacity, New Formats
The newly created clean room area of 222 square feet complements the existing clean room capacities of 650 square feet. State-of-the-art injection molding machines with clamping forces of up to 900 tons, along with an innovative machine concept featuring encapsulated lubrication, ensure that even large-format pharmaceutical packaging can be produced under the highest cleanliness standards. The precise manufacturing in DIN EN ISO class 7 and GMP-compliant environments provides customers with even greater product safety and reliability. The injection-molded parts are removed from the mold by robots, inspected by a camera, and then stacked. Automated guided vehicles (AGVs) autonomously and safely transfer them to the packaging machine.
Secure Processes, Seamless Tracking
The commissioning of the new fully automatic packaging system was another milestone in clean room production at Pöppelmann FAMAC®. In the packaging process, the items are sealed in a clean room bag and provided with an RFID label. This label contains complete batch information and is digitally carried along and read in all subsequent process steps. A mandatory double bagging follows before the product passes through the so-called "RFID gate.” This ensures that no items with differing batch information get into the same carton. This way, Pöppelmann FAMAC® achieves a significant increase in process safety and simplifies traceability—real added value in highly regulated production environments. In the future, customers will also be able to capture the data from the RFID labels upon receipt of goods to automate their own processes.
Product Carbon Footprint (PCF): Optimizing Environmental Balance
Given the growing importance of greenhouse gas emissions (GHG) in the product lifecycle, Pöppelmann FAMAC® also supports customers from the pharmaceutical industry and medical technology in designing their products in an environmentally and climate-friendly manner. As part of the strategic initiative for resource conservation and climate protection, PÖPPELMANN blue®, the plastics specialist analyzes the Product Carbon Footprint (PCF), meaning the total sum of all greenhouse gas emissions in the "Cradle-to-Gate" accounting space, from raw material extraction to the Pöppelmann factory gate. Through a non-binding consultation, further optimization potentials for the PCF can then be identified together with the customer.
Next Expansion Step Already Initiated
The clean room offering in Lohne is further strengthened by ongoing expansion: Currently, the next expansion phase under the working title "HORIZON" with an additional 500 square feet is in progress. This will allow for multi-stage manufacturing processes with subsequent assembly procedures under optimal clean room conditions in the future. "We are relying on forward-looking technology, even more capacity, and automated processes, creating real value for our customers through higher safety and efficiency," explains Michael Dultmeyer, Sales Manager Pharma-Medical. "The comprehensive digitalization of our processes and the planned expansion are proof that we are continuously working on optimizing our production processes."
Learn more.
Image:
More opportunities for the pharmaceutical industry and medical technology: Pöppelmann FAMAC® significantly expands clean room capacities and relies on fully automated processes.
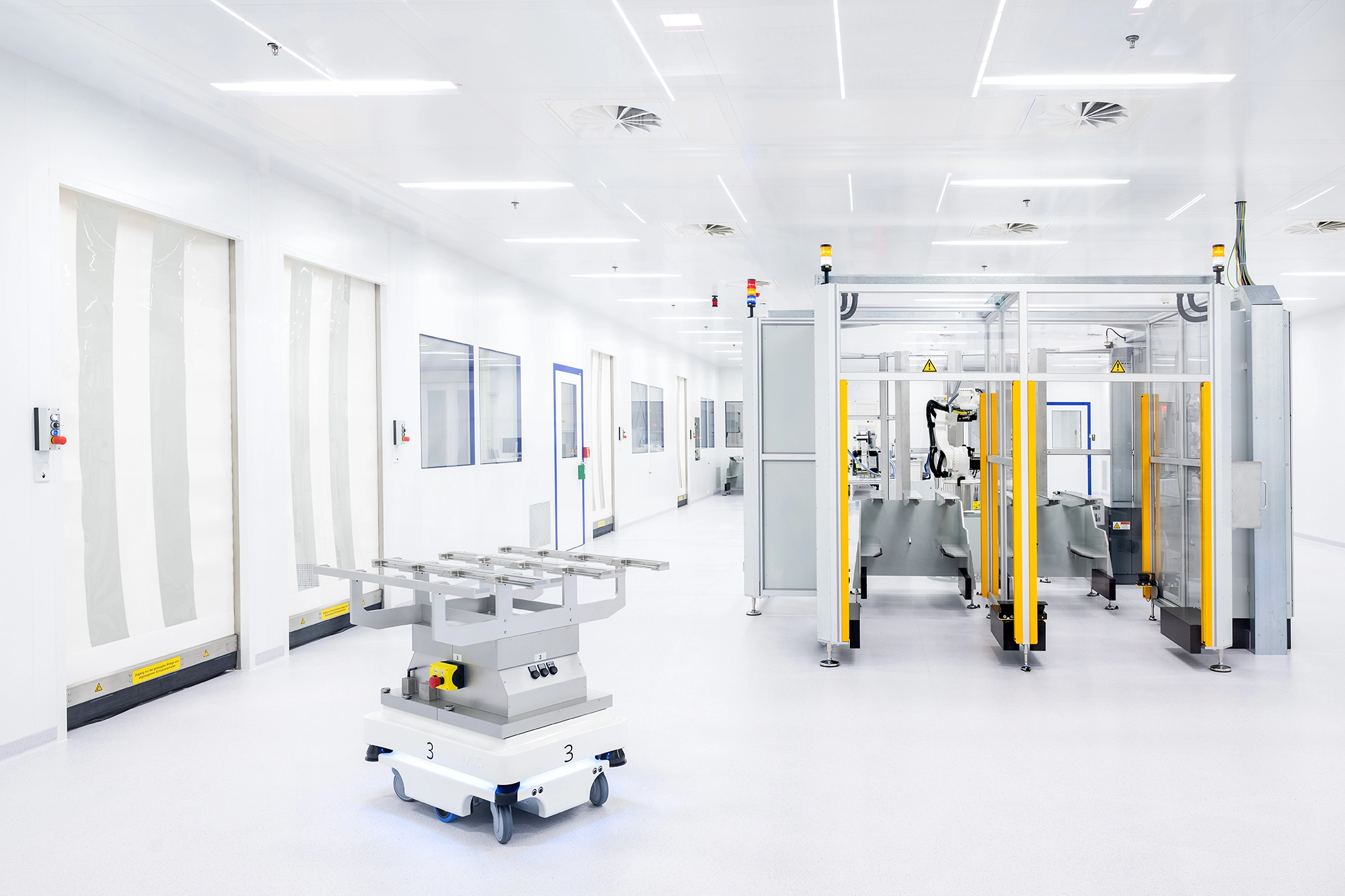