Stories
Story
Schwarz ist out #pflanztöpfe #recycle
Im Januar 2025 flog die Farbe Schwarz endgültig aus dem TEKU® Standardprogramm. Ein Meilenstein. Damit ist die komplette Produktpalette nun vollständig kreislauffähig: Trays und Töpfe, Anzuchtpaletten und Blumenampeln. Wertvolles Material bleibt für viele Produktleben erhalten. Das ist echte Kreislaufwirtschaft – und vermindert Treibhausgasemissionen. Kunden profitieren nun von einem vollständig kreislauffähigen Produktprogramm.
Manchmal liegt ein Thema in der Luft und ein eher beiläufig geäußerter Gedanke wird plötzlich zum Gamechanger. TEKU® Divisionsleiter Sven Hoping erinnert sich: „Es war 2017, in einer Besprechung in kleiner Runde. Damals stand plötzlich die Frage im Raum: Wäre es nicht cool, wenn das Material für unsere Pflanztöpfe aus dem Gelben Sack kommt?“
Zu diesem Zeitpunkt hatte TEKU® bereits mehr als vierzig Jahre Erfahrung mit der Verarbeitung von Rezyklaten zur Herstellung von Pflanztöpfen. Doch handelte es sich bis dahin beinahe ausschließlich um Produktionsreste. Diese sogenannten Post-Industrial-Rezyklate (PIR) können fast wie Neuware relativ einfach wieder in die Herstellung neuer Waren einfließen. Denn in der Regel sind sie sauber und sortiert.
Ganz anders verhält es sich mit den Abfällen von Kunststoffprodukten, die nach Gebrauch entsorgt werden – wie zum Beispiel Verpackungen. Sie landen im Gelben Sack oder der Gelben Tonne und müssen vor ihrer Weiterverarbeitung zu Post-Consumer-Rezyklat (PCR) gereinigt, sortiert und vor dem erneuten Einsatz in der Produktion hinsichtlich ihrer Materialeigenschaften genau analysiert werden. Doch um PCR ohne Abstriche am Qualitätsanspruch nutzen zu können, ist technologisches Know-how und Freude an Tüfteleien notwendig.
Pöppelmann macht blau
Doch genau das liegt in der DNA der Material- und Prozessexperten im Unternehmen. Kaum ein Jahr später sorgt TEKU® im Januar 2018 auf der internationalen Leitmesse des Gartenbaus IPM für Aufsehen. Am Messestand werden blaue Pflanztöpfe präsentiert, hergestellt aus PCR und recyclingfähig. Das Interesse ist riesig.
Mit diesem Messeauftritt hat Pöppelmann neue Standards für nachhaltige Kunststoffverarbeitung gesetzt und sich als Pionier der Kreislaufwirtschaft in der Branche positioniert. Auch unternehmensintern: Im gleichen Jahr wird die strategische Unternehmensinitiative PÖPPELMANN blue® ins Leben gerufen. Hier laufen die Fäden zusammen, um unternehmensweit Produktkonzepte für die Kreislaufwirtschaft zu entwickeln. Maxime: Das Material Kunststoff ist viel zu wertvoll, um nur einmal genutzt zu werden.
Doch warum sind die Töpfe blau, warum heißt die Unternehmensinitiative PÖPPELMANN blue®? Die Inspiration zu dieser Farb- und Namensgebung gab das Circular-Economy-Modell der Ellen MacArthur Foundation. Es unterscheidet zwei Rohstoffkreisläufe: Die Farbe Grün kennzeichnet den biologischen Kreislauf organischer Rohstoffe, die Farbe Blau den technischen Kreislauf von Materialien wie Metall oder Kunststoff von der Produktion bis zur Wiederverwertung.
Nur nicht schwarzsehen
Es gibt noch einen zweiten Grund für die Farbgebung der Töpfe. In der Gartenbaubranche gelten bis dahin schwarze Pflanztöpfe als beste und günstigste Option für den optimalen Pflanzenwuchs. Lichtundurchlässigkeit ist dabei ein wesentlicher Faktor. Der Nachteil: Die Nah-Infrarot-Detektoren in den Sortieranlagen der Dualen Systeme können schwarze Kunststoffe nicht ausreichend erkennen. Darum landen schwarze Pflanztöpfe meist bei den unsortierbaren Verpackungsresten – und damit nach lediglich einmaligem Gebrauch in der energetischen Verwertung.
Das macht deutlich: Die Verwendung von Rezyklaten ist nur der erste Schritt auf dem Weg zur Circular Economy. Um den Kreislauf zu schließen, muss das Produkt selbst auch recyclingfähig sein. Darum spielt die Farbwahl eine große Rolle. Und darin steckt gleichzeitig die Herausforderung, auch mit bunten Töpfen alle Bedingungen für den optimalen Pflanzenwuchs und die Prozessanforderungen in den Gartenbaubetrieben zu erfüllen.
Eine enge abteilungsübergreifende Zusammenarbeit, um die unternehmensweite Expertise zusammenzuführen ist seit jeher bei Pöppelmann die Antwort auf Herausforderungen wie diese.So folgen ständige Verbesserungen in Technologie und Produktionsprozessen. 2021 stellt TEKU® die ressourcenschonenden Pflanztöpfe der Kategorie Circular360 vor – in einer großen Palette an Trendfarben, hergestellt aus PCR und recyclingfähig bei der Entsorgung im Gelben Sack, lichtundurchlässig und UV-beständig.
Ohne schwarz konsequent nachhaltig
Mit dem Verzicht auf schwarze Kunststoffe im Standardprogramm hat sich TEKU® jetzt entschieden für Klimaschutz und Ressourcenschonung positioniert. TEKU® Verkaufsleiter Arno Zerhusen und Area Sales Manager Dirk Moormann sind stolz darauf, dass dieser Meilenstein nun erreicht ist. „Unser Ziel war und ist es weiterhin, die hohen Ansprüche unserer Kunden an Qualität und Effizienz zu erfüllen und gleichzeitig mit unseren Produkten mehr Klimaschutz und Ressourcenschonung zu erreichen“, sagt Arno Zerhusen.
Das ist im Übrigen nur möglich mit sauberen Recyclingströmen. Dirk Moormann erklärt, wie TEKU® das richtige Material in die Produktionshallen lenkt: „Die Zulieferer sind verpflichtet, reine und wiederverwertbare Rohstoffe zu liefern, die keine nicht-recyclingfähigen Bestandteile, wie schwarzes Material, in den Recyclingprozess einschleusen. Kunden können darauf vertrauen, dass unsere Produkte aus genau diesen Materialien gefertigt wurden. Unabhängige Zertifizierungen wie der Blaue Engel, cyclos-HTP und RecyClass garantieren die Erfüllung der strengen Umweltstandards.“
Simon Lambrecht, Produktmanager in der Entwicklung TEKU®, verweist auf die nächsten Schritte: „Wir werden an diesem Punkt nicht stehen bleiben. Gemeinsam mit unseren Partnern möchte wir weitere Materialströme erschließen, um wertvolle Rohstoffe im Kreislauf zu halten.“ Die Kreislaufwirtschaft könne nur im Bündnis mit allen Akteuren entlang der Lieferkette verwirklicht werden, betont er. „Wir sind auf Partner angewiesen, die dasselbe Ziel verfolgen. Allein funktioniert es nicht.“ Ein Beispiel: TEKU® steht im engen Kontakt mit Lieferanten, um gemeinsam geeignete Materialien zu finden, zu testen und in den Kreislauf zu bringen.
Der Mehrwert dieses Einsatzes für Klimaschutz und Ressourcenschonung lässt sich in Zahlen bemessen: Der CO2-Fußabdruck eines recyclingfähigen Pflanztopfs PCR vermindert sich gegenüber einem Topf aus Neuware um 25 Prozent.
Divisionsleiter Sven Hoping sieht den 2017 eingeschlagenen Weg sowohl unter ökologischen als auch wirtschaftlichen Nachhaltigkeitsfaktoren im Markt bestätigt. Er sagt: „Immer mehr Unternehmen der ‚grünen Branche’ wollen auch ihre Produktionsprozesse nachhaltiger gestalten. Hier setzen wir an und unterstützen den professionellen Gartenbau mit modernen Produkten, die ein optimales Pflanzenwachstum erreichen und dabei die Umwelt und das Klima schonen.“
Story
Wirtschaftlichkeit und Nachhaltigkeit in Einklang #verpackung #5p
Wirtschaftlichkeit und Nachhaltigkeit in Einklang #verpackung #5p
Wir sind davon überzeugt, dass wirtschaftlicher Erfolg und Nachhaltigkeit keine Widersprüche darstellen. Vielmehr sehen wir in der Verknüpfung dieser beiden Aspekte den Schlüssel zu zukunftsfähigen Innovationen, die sowohl ökonomisch rentabel als auch umweltfreundlich sind.
Ein herausragendes Beispiel dafür ist die Neugestaltung eines Handelsmarkenbechers für Kräuterquark, die unser Geschäftsbereich FAMAC® in einem Gemeinschaftsprojekt mit der DMK Group entwickelte.
Der Erfolg dieses Projekts zeigt eindrucksvoll, wie sich durch intelligente Anpassungen an bewährten Verpackungslösungen wertvolle Ressourcen einsparen lassen. Die materialreduzierte Neugestaltung des Quarkbechers überzeugte auch die Jury des Deutschen Verpackungspreises 2024: DMK und Pöppelmann FAMAC® wurden für dieses innovative Projekt auf der Branchenmesse Fachpack in Nürnberg in der Kategorie Wirtschaftlichkeit ausgezeichnet.
Unsere ganzheitliche Sichtweise basiert auf fünf gleichberechtigten Fragen. Lesen Sie, wie wir sie bei dieser Verpackung beantwortet haben:
Lösen wir wirksam ein echtes Problem?
Der überarbeitete Quarkbecher musste die bestehende Funktionalität beibehalten, aber ressourcenschonender gestaltet werden. Das Ergebnis: Durch konstruktive Anpassungen in der Gestaltung der Becherwand bleibt die Stabilität der Verpackung auch bei reduziertem Materialeinsatz erhalten.
Rechnet sich diese Lösung für uns und unsere Partner?
Weniger Materialeinsatz bedeutet nicht nur geringere Produktionskosten, sondern auch optimierte Logistik und damit wirtschaftliche Vorteile für alle Beteiligten, inklusive Reduzierung der Gebühren für die Dualen Systeme. Die Jury des Deutschen Verpackungspreises hob hervor, dass zur Herstellung 20 Prozent weniger Kunststoff (Polypropylen) benötigt wird. Zudem passen nun 50 Prozent mehr Becher in in eine Mehrweg-Transportbox, was die Effizienz in der Logistik deutlich steigert. Durch den reduzierten Stapelabstand passen zudem 50 Prozent mehr Becher in die Magazine der Abfüllanlagen, wodurch sich auch die Effizienz im Abfüllprozess erhöht hat.
Haben wir einen Prozess, der schnell, effizient und sicher funktioniert?
Die Anpassung des Spritzgussverfahrens sorgt dafür, dass die Versiegelung des Bechers nach dessen Befüllung trotz der dünneren Wandstärke reibungslos läuft. Erreicht wurde dies durch eingebrachte Stege an den Innenwänden des Bechers, die den Stauchdruck ausgleichen. Sie sind für den Konsumenten nicht sichtbar, aber mit großer Wirkung: Diese Überarbeitung des Designs spart mehr als 20 Prozent THG-Emissionen im Vergleich zu markttypischen Alternativen.
Überzeugt diese Lösung alle Beteiligten und Akteure wie Kunden und Verbraucher sowie interessierte Verbände?
Der reduzierte Materialeinsatz beeinflusst die Nutzung für den Verbraucher nicht negativ, sondern steigert die Attraktivität der nachhaltigen Verpackung. Die Jury des Deutschen Verpackungspreises lobte das Projekt als spannende Erfolgsgeschichte und würdigte insbesondere die partnerschaftliche Zusammenarbeit zwischen DMK und Pöppelmann FAMAC®.
Ist diese Lösung öko-effizient?
Durch die Einsparung von Kunststoff trägt der neue Becher aktiv zur Reduzierung von CO2-Emissionen bei. DMK hatte bereits zuvor den herkömmlichen Stülpdeckel bei ausgewählten Quarkprodukten abgeschafft und damit erhebliche Mengen an Kunststoff eingespart. Mit der Optimierung des Spritzguss-Bechers wurde ein weiterer wichtiger Schritt in Richtung Ressourcenschonung gemacht.
Dieses Beispiel zeigt, dass nachhaltige Produktlösungen nicht nur möglich, sondern auch wirtschaftlich sinnvoll sind. Mit harter Arbeit, Akribie und der Bereitschaft zu Veränderungen entwickeln wir Lösungen, die den Markt überzeugen und gleichzeitig einen Beitrag zum Klimaschutz leisten.
Story
Nachhaltigkeit in der Medizintechnik:
Neues Design reduziert THG-Emissionen #medinzintechnik #logistikoptimierung
Nachhaltigkeit in der Medizintechnik:
Neues Design reduziert THG-Emissionen #medinzintechnik #logistikoptimierung
Wer im Geschäftsfeld Medizintechnik aktiv ist, muss höchste Anforderungen erfüllen. Schließlich geht in diesem Bereich oftmals um Menschenleben. Zum Beispiel bei Patienten, die beatmet werden müssen. Mike Landwehr, stellvertretender Vertriebsleiter FAMAC® Pharma-Medical, betont: „Sicherheit und Leistung stehen selbstverständlich an erster Stelle.“
Das heißt: Hier lässt sich nicht einfach einmal schnell ein Fertigungsprozess verändern oder ein Werkstoff austauschen. Auch die Verwendung von Recyclingmaterialien ist in vielen Fällen nicht möglich. Dennoch stellt sich auch FAMAC® Pharma-Medical der Herausforderung, den nachhaltigen Einsatz von Ressourcen voranzutreiben.
Mit Erfolg. Dies zeigt das Beispiel der Zusammenarbeit von FAMAC® Pharma-Medical mit Drägerwerk AG & Co. KGaA zur Entwicklung von Gehäuseteilen für einen HME-Atemsystemfilter. Diese Filter minimieren das Risiko der Übertragung von Infektionen, indem sie Viren und Bakterien bei der klinischen Beatmung filtern und die Atemluft der Patienten anfeuchten. Sie werden in der Anästhesie und der Intensivmedizin eingesetzt.
Bei der Entwicklung der Atemwegsfiltergehäuse hatte das FAMAC® Team verschiedene Vorgaben des Kunden zu beachten. Dazu gehörte die quadratische Auslegung des Designs anstelle der früheren runden Form. Mike Landwehr: „Diese Vorgabe konnten wir mit weiteren Verbesserungen verbinden. Wir überzeugten mit unserem Vorschlag, wie mehr Teile in eine Verpackung passen.“ Nun ermöglicht die neue Variante eine platzsparende Stapelbarkeit der Teile und somit deutliche Optimierungen in Logistik, Transport, Lagerung und Verpackung. Hinzu kommt, dass durch die viereckige Gestaltung beim Filtermaterial weniger Verschnitt anfällt.
Das Konzept des Eco-Designs ist für alle Entwicklungsteams bei Pöppelmann Dreh- und Angelpunkt ihrer Arbeit. Dieses Konzept ist geprägt von einem ganzheitlichen Blick auf die Anforderungen – und von der Bereitschaft, Aufgaben aus verschiedenen Perspektiven anzugehen und neu zu denken. Dabei werden die Umweltauswirkungen eines Produktes entlang seines gesamten Lebensweges berücksichtigt und so gering wie möglich gehalten.
So wie in diesem Fall: Die Vorgaben des Kunden konnten mit weiteren Vorteilen verknüpft werden – die allesamt zur Verminderung der Treibhausgas-Emissionen beitragen. Dazu gehört auch die Verwendung von Materialresten, die während des Produktionsprozesses in der Kunststoffverarbeitung anfallen („Angüsse“). Was früher im Kunststoffabfall landete, wird jetzt wieder eingeschmolzen und neu genutzt.
So bringt das neue Design des Gehäuseteils heute noch mehr Vorteile: Die eingesetzte Angussrückführung in der Herstellung führt dazu, dass in Bezug auf die jährliche Produktionsmenge 6 Prozent an THG-Emissionen reduziert werden können. Zudem ermöglicht die quadratische Ausführung eine platzsparende Stapelbarkeit der Teile und somit eine deutliche logistische Optimierung bei Verpackung, Lagerung und Transport: Wo vorher lose geschüttet 4.800 Teile auf einer Palette Platz fanden, sind es nun 7.392 Teile. Damit konnten wir die THG-Emissionen im Bereich der Logistik um 3,3 Tonnen CO2e reduzieren – das entspricht 32 Prozent; ebenfalls bezogen auf die Produktionsjahresmenge.
Die Neugestaltung der Atemwegsfilter überzeugt nicht nur in Sachen Ressourcenschonung: Für das bereits im Markt eingeführte Produkt wurde Dräger mit einem Red Dot Design Award ausgezeichnet. In der Begründung der Jury heißt es: „Bei der ausgeklügelten Gestaltung dieser Atemschutzfilter wurde in hohem Maße Wert auf den Schutz der Patienten und des medizinischen Personals gelegt.“
Mehr Infos auf der Pöppelmann-Webseite:
Praxisbeispiel-Logistikoptimierung-Dräger
Story
Im Turbogang Richtung Kreislaufwirtschaft unterwegs #automotive #recycle
Im Turbogang Richtung Kreislaufwirtschaft unterwegs #automotive #recycle
Der Weg zu einer echten Kreislaufwirtschaft gehört zu den entscheidenden strategischen Herausforderungen auch in der Automobilindustrie. Lange Zeit galt es für technisch nicht realisierbar, im Autobau Post-Consumer-Rezyklate zum Einsatz zu bringen. Doch wir haben es geschafft. Und wir stehen bereit, die geplanten gesetzlichen Vorgaben der EU zum Rezyklateinsatz im Autobau (End of Life Vehicles Directive; Altautoverordnung) gemeinsam mit unseren Kunden umzusetzen.
Frank Schockemöhle, Leiter des Technologiemanagements bei Pöppelmann, erinnert sich noch gut an eine Tagung im Juni 2022: „Ich war eingeladen, Einblick in unsere Arbeit zum Thema Rezyklateinsatz im Autobau zu geben. Mein Vorredner schloss seinen Vortrag sinngemäß mit den Worten: ‚Bis Post-Consumer-Material im Auto ist, dauert es noch zehn Jahre.‘ Dann übernahm ich das Mikrofon und konnte sagen: Vielen Dank. Mein Thema ist, dass wir bereits in Serie sind.“
Denn die Pöppelmann-Division K-TECH® beschäftigte sich zu diesem Zeitpunkt bereits seit Langem mit Konstruktion und Entwicklung von Autobauteilen für die Kreislaufwirtschaft. 2018 war die strategische Nachhaltigkeitsinitiative PÖPPELMANN blue® ins Leben gerufen worden. Von da an gaben die Themen Kreislaufwirtschaft und Ressourcenschonung unternehmensweit die Richtung vor. Maxime: „Kunststoff ist ein viel zu wertvolles Material, um nur einmal genutzt zu werden.“
Von nun an standen Post-Consumer-Rezyklate (PCR) im Blickpunkt des Interesses: Kunststoffe, hergestellt aus nach Gebrauch entsorgten Produkten, wie beispielsweise wieder aufbereiteten Abfällen aus dem gelben Sack. Bereits bevor es losging mit PÖPPELMANN blue®, hatte TEKU® seit mehr als 50 Jahren Pflanztöpfe aus Post-Industrial-Rezyklaten (PIR), also Produktionsresten, hergestellt. Dieses Know-how war nach Gründung der Unternehmensinitiative der Ausgangspunkt für die schrittweise Umstellung der TEKU® Produktion auf Post-Consumer-Rezyklate.
So wirkt ein besonderer Pöppelmann-Effekt auf dem Weg zu kreislauffähigen Produkten als Beschleuniger: Durch die vier Geschäftsbereiche, die in ganz unterschiedlichen Märkten agieren, sind Know-how und Kompetenz für Kunststoffe im Unternehmen breit gefächert. Ein Vorteil, der K-TECH® in die Lage versetzte, bei der Entwicklung des ersten Autobauteils aus Post-Consumer-Rezyklat den Turbogang einzulegen. Frank Schockemöhle: „Im März 2020 hatten wir die Idee zur Materialentwicklung eines PCR PP GF30. Und im Dezember 2020 erhielten wir die Serienfreigaben für die Halter Soundgeneratoren.“
Höchste Sicherheits- und Qualitätsansprüche sind zu erfüllen
Die Verwendung von Kunststoffen aus Verbraucherabfällen war in der Pöppelmann-Division damals Neuland. Aus gutem Grund: Im Automobilbau gelten höchste Sicherheits- und Qualitätsansprüche, und zwar weltweit auf dem gleichen Level. Die geforderten Materialeigenschaften sind technologisch komplex; Autobauteile müssen hohen Belastungen standhalten. Wer in dieser Branche mit Rezyklaten arbeiten will, muss die Eigenschaften gebrauchter Kunststoffe ebenso genau und nachweisbar definieren können wie für Neuware.
All dies floss ein in die Überlegungen darüber, welches Bauteil für die PCR-Premiere bei K-TECH® geeignet sein könnte. Schließlich fiel die Wahl auf die Halterung für Soundgeneratoren. Sie simulieren Motorengeräusche, um Radfahrer und Fußgänger rechtzeitig vor den fast geräuschlosen Elektrofahrzeugen zu warnen. Der Halter wird außen an der Karosserie angebracht. Dies erleichterte den Einstieg in die Aufgabenstellung. „Denn im Exterieurbereich sind die Maßgaben hinsichtlich der Geruchsbelastungen nicht so hoch wie im Innenraum“, erklärt Frank Schockemöhle.
Materialumstellung gelingt gemeinsam mit Lieferanten und Kunden
Weitgreifende Innovationen wie diese sind nur mit Partnern entlang der gesamten Lieferkette zu realisieren. Dies galt auch in diesem Fall: Bevor dem Kunden die Materialumstellung vorgeschlagen wurde, entwickelte und testete K-TECH® gemeinsam mit einem Lieferanten geeignete Post-Consumer-Rezyklate.
Frank Schockemöhle blickt zurück: „Bereits seit 2012 haben wir bei K-TECH® PIR-Material verarbeitet und erste Erfahrungen gesammelt. Seitdem konnten wir unser Wissen rund um die Qualifikation von Rezyklaten immer weiter ausbauen. Diese Erfahrungen flossen dann zusammen mit den Erfahrungen aus der TEKU® Produktion ein in unsere ersten PCR-Lösungen im Automobilbereich. Wir mussten auch herausfinden, wie wir das Material aufbereiten konnten, um die entsprechende Qualität zu bekommen und wieder verarbeitbar zu machen.“
Erst als die Ergebnisse dieser Tests überzeugten, stellten Frank Schockemöhle und sein Team zusammen mit den Vertriebskollegen dem Kunden die Idee vor. „Wir hatten die entsprechenden Nachweise dabei, um zu zeigen, dass die Materialumstellung von Neuware auf PCR funktioniert. Und so haben wir es dann wirklich innerhalb von neun Monaten geschafft, ein bestehendes Serien-Bauteil aus Neuware auf Post-Consumer-Material umzustellen.“ Ein Rekordtempo in der Branche.
In Scope 3 ist Kreislaufwirtschaft der größte Hebel
Und rasant geht die Entwicklung weiter. Der Druck steigt. Die Notwendigkeit, Treibgasemissionen zu reduzieren, um die katastrophalen Auswirkungen des Klimawandels zumindest zu begrenzen, ist wissenschaftlich belegt. Produktionsmaterial, das im Kreislauf zirkuliert, trägt zur Reduzierung der Emissionen der Kategorie Scope 3 bei. Das sind die indirekten Emissionen eines Unternehmens, auf die es keinen direkten Einfluss hat, da sie durch eingekaufte Produkte – wie beispielsweise eingekaufte Kunststoffe aus Neuware – und im Nachgang durch die Entsorgung der verkauften Produkte nach Gebrauch entstehen.
In Scope 3 ist die Kreislaufwirtschaft der größte Hebel zur Verminderung. Denn so wie diese Emissionen entlang der gesamten Lieferkette entstehen, sind sie genauso entlang der gesamten Lieferkette am wirksamsten zu reduzieren. Ein Beispiel: Wenn ein Kunststoffunternehmen Post-Consumer-Rezyklate in der Produktion einsetzt, wirkt sich das sowohl auf die eigene Klimabilanz als auch auf die des Kunden positiv aus.
Gleichzeitig treibt der Gesetzgeber die Kreislaufwirtschaft mit neuen Verordnungen und Richtlinien voran. So blickt die Autobranche aktuell nach Brüssel: Hier beraten EU-Parlament und Europäischer Rat über einen Entwurf der EU-Kommission für ein Update der Alt-Auto-Verordnung (ELV). Einer der Vorschläge darin sieht vor, dass 25% der in Fahrzeugen verwendeten Kunststoffe aus Post-Consumer-Rezyklaten (PCR) stammen müssen – und davon wiederum mindestens 25% direkt aus Altfahrzeugen.
Die Richtung ist vorgegeben. Der Einsatz von PIR und PCR wird auch im Automobilbau in den kommenden Jahren an Bedeutung gewinnen. Dies erfordert Weiterentwicklungen in Abfallerfassung und-sortierung, Recycling- und Verarbeitungsverfahren, den Vorgaben für Lastenhefte und Qualitätsbewertungen. Auch die konsequente Umsetzung von zirkulärem Design gehört zu den Voraussetzungen für den Erfolg.
Wir warten nicht ab, was kommt, sondern wir gehen der Kreislaufwirtschaft entgegen. Gemeinsam mit unseren Kunden und Lieferanten suchen und finden wir Leuchtturmprojekte, die zeigen: Der Einsatz von Post-Consumer-Rezyklate im Automobilbau ist möglich – hier und heute. Jüngstes Beispiel aus der Division K-TECH® ist die Aufsatzkonsole für Wagenheber, die bereits jetzt zu 100% auf die geplante Neufassung der Alt-Auto-Verordnung einzahlt.
Frank Schockemöhle ist zuversichtlich, dass K-TECH® auf dem richtigen Weg ist: „Wir haben das gesamte Thema Design for Circularity fest in der Konstruktions- und Entwicklungsabteilung implementiert. Bei jedem neuen Projekt überlegen wir: Wie erfüllen wir die Wünsche und Forderungen des Kunden mit den besten Lösungen für Materialreduzierung, Kreislaufwirtschaft und Klimaschutz?“ Im Blick nach vorn sagt er: „Ein wichtiges Thema der Zukunft wird die Reduzierung der Materialvielfalt sein. Wenn das gelingt, haben wir es in den nächsten Jahren auch viel einfacher, diese Materialien wieder zu größeren Mengenströmen zusammenzuführen und wieder zu recyceln, um daraus wieder gute Kunststoffe zu machen. So können wir dem Kunden gute Lösungen für seinen Weg in Richtung Klimaschutz aufzeigen. So sichern wir uns heute die Materialien von Morgen.“
Story
80% der Neuaufträge bringen Post-Consumer-Rezyklate in den Kreislauf #schutzelemente #recycle
80% der Neuaufträge bringen Post-Consumer-Rezyklate in den Kreislauf #schutzelemente #recycle
Ob Automobilindustrie, Maschinenbau oder Baubranche: Die Schutzelemente der Pöppelmann-Division KAPSTO® sind in vielen Industriebereichen im Einsatz. Sie schützen funktionsentscheidende und sicherheitsrelevante Bauteile während der Fertigung, der Lagerung und des Transports. Gefertigt aus hochwertigen Kunststoffen, sind die KAPSTO® Artikel jedoch oft nur sehr kurz im Gebrauch, manche nur wenige Minuten. Dies war im Oktober 2022 der Ausgangspunkt für die größte Programmerweiterung, die es je bei KAPSTO® gab. Mit der schrittweisen Umstellung des KAPSTO® Normprogramms auf Schutzelemente aus recycelten gebrauchten Kunststoffprodukten bleibt jetzt wertvolles Material langfristig im Kreislauf.
Thorsten Koldehoff, Globaler KAPSTO® Vertriebsleiter, erinnert sich: „Natürlich haben die Ziele der strategischen Unternehmensinitiative PÖPPELMANN blue® auch unsere Kolleginnen und Kollegen begeistert. Wer möchte nicht daran mitwirken, zu Klimaschutz und Ressourcenschonung beizutragen? Gerade für kurzlebige Anwendungen ist es nicht hinnehmbar, dass hochwertiger Kunststoff nur einmal genutzt wird.“
Der Name der Pöppelmann-Division KAPSTO® steht für „Kappen und Stopfen“ – und darin steckt zugleich ein Stück Firmengeschichte. Denn mit der Fertigung einer Griffkappe, die auf einen Korken aufgesetzt wurde, begann 1955 die Kunststoffära des Unternehmens, das als Korkfabrik gegründet wurde.
Bei Schutzelementen aus dem KAPSTO® Portfolio scheint es sich auf den ersten Blick um relativ einfache Produkte zu handeln. Doch das täuscht. Schließlich müssen sie heute in vielen Industriebereichen zuverlässig hochempfindliche Technik während komplexer Produktionsprozesse schützen. Die Anforderung an Qualität und Materialeigenschaften sind hoch.
Wer darüber nachdenkt, wie Materialkreisläufe geschlossen werden können, muss wissen: Dies funktioniert nur mit der Wiederverwertung von Post-Consumer-Rezyklaten (PCR). PCR wird hergestellt aus nach Gebrauch entsorgten Kunststoffprodukten, zum Beispiel aus Verpackungsabfällen, die in der gelben Tonne gesammelt werden. Echte Kreislaufwirtschaft bedeutet, dass aus gebrauchten Produkten wieder neue Produkte werden, und zwar auf gleicher oder höherer Qualitätsstufe.
Darauf sollte jeder achten, wer von „Rezyklaten“ liest. Denn nicht selten sind dann Post-Industrial-Rezyklate (PIR) gemeint. Dabei handelt es sich um Reste aus der Produktion, also Material, das noch nicht in Gebrauch war. Natürlich trägt auch die Verarbeitung von PIR zur Ressourcenschonung bei, weil sie den Verbrauch von Neuware vermindert. Doch PIR schließt genauso wie Neuware erst dann den Materialkreislauf, wenn es mindestens einmal in Gebrauch, entsorgt und dann wiederverwertet wurde. Denn dies ist die Grundidee der Kreislaufwirtschaft: Materialien zirkulieren für viele Produktleben im Kreislauf und vermindern so beispielsweise in der Kunststoffbranche den Verbrauch fossiler Rohstoffe.
Und genau dies war das erklärte Ziel von KAPSTO®, das die beteiligten Teams seit 2018 konsequent ansteuerten. „Die Umstellung auf PCR brachte komplexe Aufgaben mit sich, denn die Materialeigenschaften variieren“, erklärt Holger Ommen, PCR-Experte im KAPSTO-Vertrieb, im Rückblick. „Bis zum Erfolg mussten wir einige Lernprozesse durchlaufen.“ Umfangreiche Tests und Analysen waren notwendig, um beispielsweise Fragen zu Temperaturbeständigkeit zu klären. Auch für die Produktion gab es Herausforderungen bei der Verarbeitung von PCR. So sind die Fließeigenschaften schlechter und deren Schwankungen größer im Vergleich zur Neuware.
Schließlich startete im Herbst 2022 „die größte Programmerweiterung, die es je bei KAPSTO® gab“, wie Vertriebsleiter Thorsten Koldehoff den Materialwechsel beschreibt. „Nach aufwändiger Entwicklungsarbeit konnten wir im Herbst 2022 zunächst 1900 Artikel als Variante aus nachhaltigem Kunststoff standardmäßig verfügbar machen.“ Heute sind es insgesamt mehr als 2000 Artikel, die aus dem KAPSTO® Standardprogramm als PCR-Variante bestellt werden können.
Das Ergebnis: Der Kunststoffanteil der nachhaltigen Kunststoffkappen und Kunststoffstopfen besteht zu 100% aus PCR. Dabei verwendet KAPSTO® das Recyclingmaterial PCR-Polyethylen (PCR-PE) und PCR-Polypropylen (PCR-PP). Alle KAPSTO® Produkte aus PCR-PE, PCR-PP und PCR-PE-HD tragen das Umweltzeichen Blauer Engel, das für umweltfreundliche Produkte vergeben wird und garantiert, dass die Produkte aus mindestens 80% Post-Consumer-Rezyklaten bestehen. Hinzu kommen für spezielle Farbwünsche Artikel in Recycling-Mischungen aus PCR und Neuware („Blend“), die im Vergleich zu Varianten ausschließlich aus Neuware immer noch eine deutlich geringere CO2-Belastung aufweisen.
Der überwiegende Teil der KAPSTO® Kunden habe diese Programmerweiterung begeistert aufgenommen, berichtet Holger Ommen. „Auch in diesem Fall hat sich bestätigt, dass nachhaltige Lösungen nur gemeinsam erfolgreich auf den Weg gebracht werden. Flexibilität und Offenheit gegenüber Veränderungen sind auf allen Seiten notwendig, auch bei den Kunden. Manchmal sind es Gewohnheiten, zum Beispiel bei der Farbwahl der Artikel, die sich neu einspielen müssen, manchmal ist eine durchaus aufwändige neue Artikeldokumentation notwendig“, beschreibt er eine Herausforderung.
Doch KAPSTO® überzeugte – und zwar konkret mit Zahlen, Daten, Fakten. Mit ein paar Klicks können Einkäufer mit dem Online-CO2-Rechner auf der Website ermitteln, wie sich der Ausstoß von Treibhausgasen reduziert, wenn man sich für ein Schutzelement aus PCR-Material statt aus Neuware entscheidet. „Dadurch sieht auch der Kunde direkt, welche Mehrwerte diese Artikel für seine eigene Klimabilanz bietet“, erklärt der KAPSTO® PCR-Experte. Er verweist zudem auf die Mustersendungen, die jeder Interessierte anfordern kann, um die Schutzelemente aus Post-Consumer-Rezyklat in den eigenen Prozessabläufen zu testen. „Dieses Angebot wird gern genutzt.“
Mittlerweile liefert KAPSTO® etwa 80% der Neuaufträge, für die es eine entsprechende Materialalternative im Programm gibt, in der PCR-Variante aus. Ein großer Erfolg, auch für das Ziel Kreislaufwirtschaft insgesamt. Doch der Weg ist an diesem Punkt noch längst nicht zu Ende, betont Holger Ommen. „Im nächsten Schritt wollen wir mit CapCylce ein Rücknahmesystem etablieren“, kündigt er an. „Gemeinsam mit den Kunden koordinieren wir die Rückführung gebrauchter Schutzelemente, aus deren Material wir neue Schutzelemente fertigen. So wird der Kreislauf komplett geschlossen. Wir führen bereits Gespräche mit interessierten Betrieben, die größere Mengen zurückgeben möchten.“
Thorsten Koldehoff betont, dass es viele gute Gründe für die Verwendung von kreislauffähigen Schutzelementen gibt: „Schon heute fordern OEMs den Einsatz von PCR. Zudem erwarten wir in naher Zukunft EU- und nationale Gesetzgebungen hinsichtlich der Vorgaben an Recycling-Quoten. Diese Vorgaben wären dann bereits für betreffenden Produkte erfüllt.“
Story
Die ERFOLGSGESCHICHTE PÖPPELMANN BLUE® #circular #recycle
Die ERFOLGSGESCHICHTE PÖPPELMANN BLUE® #circular #recycle
Pöppelmann gehört im Bereich der Kunststoffverarbeitung zu den Vorreitern für die Kreislaufwirtschaft. Unternehmensinterner Motor für diese Entwicklung war die Gründung der strategischen Unternehmensinitiative PÖPPELMANN blue® im Jahr 2018. Damals hatten Gesellschafter, Beirat und Geschäftsführung entschieden, ein erstes Projekt für ein kreislauffähiges Serienprodukt zu starten.
Etwa zur gleichen Zeit rüttelten Berichte über eklatante Missstände im Umgang mit Kunststoff, wie die Plastikmüllverschmutzung der Weltmeere, Mikroplastikpartikel in der Umwelt und fragwürdige Entsorgungswege von Kunststoffabfällen die Öffentlichkeit auf. Mit PÖPPELMANN blue® setzte das Unternehmen der berechtigten Kritik die eigene Überzeugung entgegen: Kunststoff ist das Material der Zukunft – wenn man richtig damit umgeht.
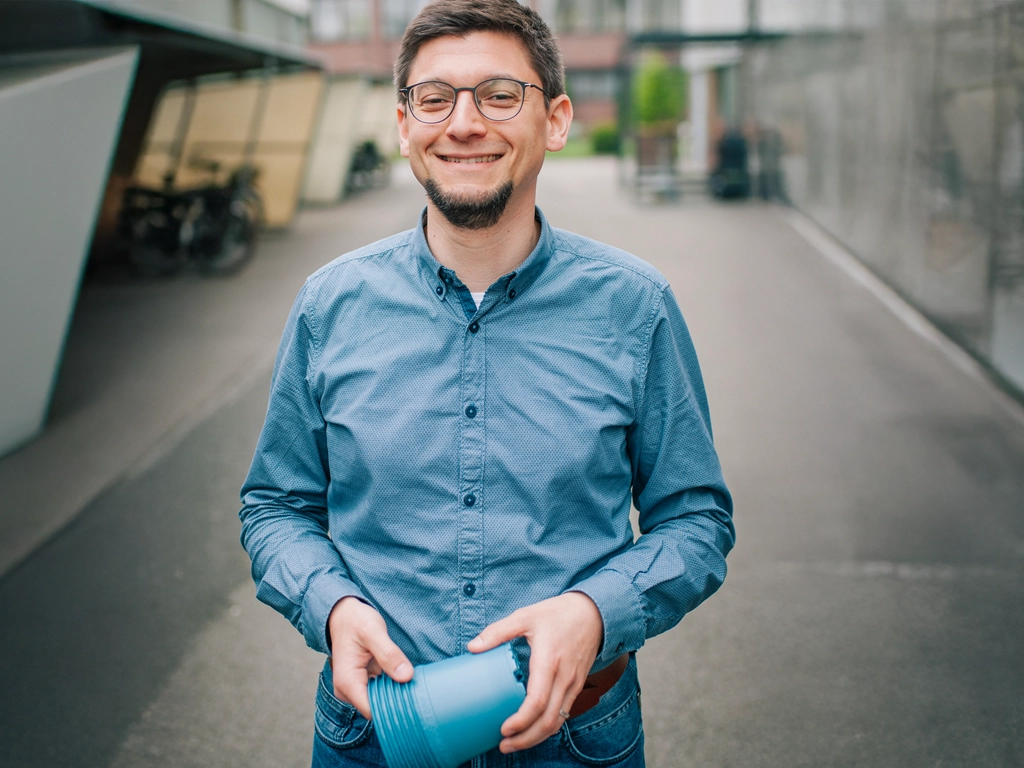
#circular
Die Strategie und Ziele der Initiative werden auf der höchsten Führungsebene des Unternehmens entwickelt: Einmal im Quartal tagt der Lenkungsausschuss PÖPPELMANN blue® mit Vertretern der Gesellschafter, Beirat, Geschäftsführung sowie Fachexperten aus den Divisionen und Zentralabteilungen.
"Wir haben Rezyklateinsatz in Serienanwendungen sehr schnell sehr weit vorangebracht“.
Zentraler Ansprechpartner der Initiative und Koordinator der Aktivitäten im Unternehmen ist Benjamin Kampmann. Er gehört als „Möglichmacher“ mit dem Fokus Ressourcenschonung und Klimaschutz zum Team MORGEN. Im Interview hat Benjamin einige Rragen rund um PÖPPELMANN blue® beantwortet.
Zunächst einmal die Frage, wie man Kunststoff überhaupt mit Nachhaltigkeit in Verbindung bringen kann. Denn der Begriff Plastik weckt ja vielfach sehr negative Gefühle. Vielen denken bei unserem Werkstoff zuerst an die Vermüllung der Weltmeere und vieler anderer Probleme wie Mikroplastik. Wäre es nicht am besten, es gäbe keinen Kunststoff mehr?
Darin steckt ja die Frage: Wäre es nicht besser, wenn es dieses oder jenes Kunststoffprodukt gar nicht gäbe? Aus ökologischer Sicht ist Verzicht immer die beste Option. Doch worauf wollen oder können wir tatsächlich verzichten? Blicken wir mal auf unser Produktportfolio bei Pöppelmann: KAPSTO® produziert Schutzelemente, die in der industriellen Fertigung und als Produktschutz unerlässlich sind. Oder der Bereich Mobilität: Wir wollen und müssen mobil sein. Kunststoff ermöglicht Leichtbaulösungen für Fahrzeugteile, die K-TECH® produziert. Lebensmittel sind unverzichtbar – und ebenso die Verpackungen, die sie vor Verderb schützen und hygienische Standards gewährleisten. Auch Medikamente sind essenziell. Beide Branchen betreffen unsere Produktion bei FAMAC®. Ebenso benötigen wir Produkte für den Gartenbau, ein Markt, den TEKU® beliefert.
Wenn wir den völligen Verzicht in all diesen Bereichen als unrealistisch betrachten, wird deutlich: Eine Welt ohne diese Produkte ist kaum denkbar. Die eigentliche Frage, die wir uns stellen sollten, ist daher die nach der Ökoeffizienz.
Was bedeutet das?
Der Begriff Ökoeffizienz beschreibt das Verhältnis zwischen Wertschöpfung und den verursachten Emissionen und Umweltauswirkungen. Ziel ist es, mit möglichst wenig Einsatz von Ressourcen und Energie eine möglichst optimale Produktlösung zu realisieren. Dazu gehört auch die Bewertung, mit welchem Material dieses Ziel am besten erreicht werden kann. Darum ist für uns das anforderungsgerechte Eco-Design Dreh- und Angelpunkt der Produktentwicklung. Dieser Gestaltungsansatz beinhaltet sehr viel mehr als Recyclingfähigkeit einer Verpackung oder die Verwendung von Rezyklaten. Im Eco-Design nehmen wir den gesamten Lebenszyklus eines Produkts in den Blick.
Wie kann man denn als Hersteller auf das gesamte Produktleben Einfluss nehmen?
Indem das Denken nicht am Werkstor aufhört, sondern Logistik, Nutzung und Entsorgung mit einbezieht. Dies gilt nicht nur bei kurzlebigen Produkten wie Verpackungen, sondern auch bei langlebigen Bauteilen zum Beispiel im Automobilbereich.
Wir wollen durch Eco-Design immer eine möglichst funktionelle und ökonomische Lösung finden. Da kommt es durchaus zu Zielkonflikten, wenn man beispielsweise in der Entwicklungsphase darüber nachdenkt, was wichtiger ist: Minimaler Materialeinsatz, der vielleicht durch einen nicht recyclingfähigen Materialaufbau erreicht werden kann? Oder die Recyclingfähigkeit?
Wie wird diese Herangehensweise im Unternehmen umgesetzt?
Zu Beginn jeder Produktentwicklung fragen wir uns zuerst: Was ist die Kernfunktion des Produktes? Und direkt im Anschluss: Wie können wir mit unserer Lösung Wirtschaftlichkeit und ökologische Nachhaltigkeit, also möglichst minimale Umweltauswirkungen, miteinander verbinden? Die Bewertung der Umweltauswirkungen ist dabei für uns ein wichtiges Kriterium. Dazu gehört unter anderem auch der CO₂-Fußabdruck. Wir arbeiten in jeder Produktentwicklung, Konstruktion und Fertigung die Vorteile unseres Materials bestmöglich heraus. So reduzieren wir Schritt für Schritt unsere Treibhausgasemissionen und nähern uns unseren Klimazielen.
Das führt uns nun zur Initiative PÖPPELMANN blue, in der diese Ziele ja definiert wurden. War es schwer, im Unternehmen das Bewusstsein für Nachhaltigkeitsthemen zu schärfen?
Die Gründung der Initiative entstand nicht im luftleeren Raum, sondern auf Grundlage eines zu diesem Zeitpunkt bereits fest verankerten Umweltmanagements. Seit 1996 beteiligen wir uns auf freiwilliger Basis am „Eco-Management and Audit Scheme“ der Europäischen Union, kurz: EMAS. Es gilt weltweit als das anspruchsvollste System für nachhaltiges Umweltmanagement. Darauf aufbauend haben wir über die Jahre weitere Managementsysteme, beispielsweise das Energiemanagement, eingeführt. Von daher standen das Thema Umweltschutz und der Anspruch, nachhaltig zu wirtschaften und sparsam mit den Rohstoffen unserer Erde umzugehen, seit jeher oben auf der Agenda.
Was gab den Anstoß, mit PÖPPELMANN blue dann zunächst der Kreislaufwirtschaft und Ressourcenschonung und ab 2022 auch dem Klimaschutz ein solches Gewicht in den strategischen Zielen zu geben?
Als wir PÖPPELMANN blue® gründeten, geschah dies im Bewusstsein der Herausforderungen durch die Plastikkrise und vor allem auch die Klimakrise. Wir wollten aktiv werden, denn wir sind überzeugt, dass wir mit unserem Material und unserer Arbeit zu neuen zukunftsfähigen Lösungen beitragen können. Dabei ist die Wiederverwertung unseres wertvollen Rohstoffs nach dem Modell der Kreislaufwirtschaft ein zentraler Aspekt. Vor diesem Hintergrund fiel 2017 in der Division TEKU® die Entscheidung, ein zirkuläres Leuchtturmprojekt zu starten. Es sollte untersucht werden, wie ein recyclingfähiger Pflanztopf gefertigt werden kann und wie für die Herstellung dieses Produkts Rezyklate aus Verpackungsabfällen, also zum Beispiel aus der gelben Tonne, genutzt werden können. Aus den ersten Produktergebnissen entwickelte sich das erste Serienprodukt aus Post-Consumer-Rezyklat: Auf der IPM 2018 konnten wir unseren blauen Pflanztopf für Küchenkräuter vorstellen. Dieser Leuchtturm wurde zur Initialzündung für die Gründung der Initiative PÖPPELMANN blue®.
Andere Unternehmen stellen für diese Themen oft eine Nachhaltigkeitsmanagerin oder einen Nachhaltigkeitsmanager ein. Wer übernimmt diese Rolle bei Pöppelmann?
PÖPPELMANN blue® ist auf der höchsten Führungsebene des Unternehmens verankert. Denn wir wollten die Nachhaltigkeit nicht in einer Abteilung isolieren. Vielmehr ist bei uns jede und jeder in seinem Bereich „Nachhaltigkeitsmanager“. Im Lenkungsausschuss der Initiative tauschen sich vierteljährlich Vertreter der Gesellschafter, des Beirates, der Geschäftsführung und Expertinnen und Experten der Zentralabteilungen und Divisionen aus. Sie vereinbaren immer wieder neue Projekte und Ziele und treiben diese kontinuierlich voran. Dieses Vorgehen ist eines der Erfolgsrezepte, wodurch wir beispielsweise das Thema Rezyklateinsatz in Serienanwendungen sehr schnell sehr weit voranbringen konnten.
Wie wird denn die Initiative im Arbeitsalltag sichtbar und auch wirksam?
Die Möglichkeit, mit der eigenen Arbeit dazu beizutragen, die Erderhitzung zu begrenzen, motiviert und begeistert auch unternehmensintern. Gleichzeitig ist ganz klar: Wir müssen mit unseren Produkten am Markt bestehen und wirtschaftlich überzeugen. Wenn wir über Kreislaufwirtschaft, Klimaschutz und Ressourcenschonung in unserer Branche sprechen, geschieht dies immer auch unter der Prämisse der Wirtschaftlichkeit. So entwickelte sich im Laufe der Zeit in den Abteilungen und Teams ein ganzheitlicher Blick auf die Anforderungen der Kunden. Wir sagen heute: Bei uns sitzen die Nachhaltigkeitsaspekte mit am Entscheidertisch. Hier wird sie gleichberechtigt mit Kriterien wie Qualität, Wirtschaftlichkeit, Prozesssicherheit und Verbrauchernutzen verhandelt.
Mittlerweile gibt es in jeder Division nicht nur Leuchtturm-Projekte im Rahmen von PÖPPELMANN blue, sondern auch Serienanwendungen, die das Thema auf die Straße gebracht und so branchenweit Maßstäbe gesetzt haben. Was waren und was sind die Voraussetzungen für diesen Erfolg?
In den Leuchtturmprojekten haben wir viele Erkenntnisse für die Entwicklung weiterer Kreislauf-Produkte gewinnen können. Um ein Beispiel zu nennen: Schon in der Produktentwicklung müssen die Designanforderungen hinterfragt werden. So können wir ganz am Anfang des Projekts auf die Verwendung von Rezyklaten in der Produktion und die Recyclingfähigkeit des Produkts Einfluss nehmen. Insbesondere für Verpackungen ist das Design for Recycling mittlerweile zum Standard geworden, oder auch: Design for Circularity. Denn bereits die Entscheidungen zu diesem frühen Zeitpunkt tragen maßgeblich zur Sicherung künftiger Materialströme bei.
Gehen denn die Kunden diesen Weg mit?
Viele Kunden kommen mittlerweile proaktiv auf uns zu, andere Kunden können wir im Laufe der Entwicklungsphase von unserem zirkulären Ansatz überzeugen. Durch unsere Herangehensweise hinterfragen wir oft ursprüngliche Produktanforderungen. In den meisten Fällen stoßen wir mit unseren Vorschlägen auf Interesse, zum Beispiel beim Thema Materialvielfalt. Die Verarbeitung von Rezyklaten erfordert Flexibilität an verschiedenen Stellschrauben. Die Maßgabe ist dabei nicht die maximale Produktivität, sondern die Abstimmung von Anwendung, Prozessen und Material für einen optimalen Kompromiss im Sinne der Kreislaufwirtschaft der Nachhaltigkeit und der Wirtschaftlichkeit.
Wie wirkt sich dieser ganzheitliche Blick auf die Klimaziele von Pöppelmann aus?
Dazu möchte ich kurz erklären, wie diese Klimaziele definiert werden. Zunächst haben wir unseren kompletten CO2-Fußabdruck – den Corporate Carbon Footprint – für das Jahr 2021 ermittelt. Auf dieser Grundlage haben wir unsere Klimaziele für 2030 nach der wissenschaftsbasierten Methode der Science Based Targets initiative (SBTi) festgelegt. Danach werden Treibhausgas-Emissionen in bestimmte Kategorien, nämlich „Scopes“, eingeteilt. In Scope 1 und Scope 2 werden die Emissionen gemessen, die direkt bei uns vor Ort entstehen, beispielsweise durch Verbrennung von Benzin, Diesel und Gas und durch den Verbrauch eingekaufter Energie. Die Scope 3-Emissionen entstehen indirekt entlang der Lieferkette, unter anderem durch eingekaufte Waren, Transporte und Entsorgung unserer Produkte, aber beispielsweise auch durch das Pendeln der Mitarbeitenden.
Und welche Klimaziele hat Pöppelmann sich nun gesetzt?
Wir haben uns 2023 gegenüber der Science Based Targets initiative (SBTi) verpflichtet, unsere absoluten Scope 1 und 2 Emissionen um 50% und unsere absoluten Scope 3-Emissionen um 25% zu reduzieren, jeweils bis 2030 im Vergleich zu 2021. Wir sind nun verpflichtet, die THG-Emissionen jährlich neu zu berechnen und zu veröffentlichen. . Die jeweils aktuellen Daten veröffentlichen wir in unserem Treibhausgasbericht. Jede unserer Abteilungen und Divisionen hat ihre eigenen strategischen Ziele formuliert, um zu diesem Klimaziel beizutragen. Zur Reduzierung der Sope 1- und Scope 2-Emissionen optimieren wir beispielsweise unseren Energieverbrauch, wir beschaffen Strom aus regionalen Windparks und wir bauen PV-Anlagen auf unseren Hallen.
Und wie sieht es aus mit den Emissionen in Scope 3? Kommt hier die Kreislaufwirtschaft ins Spiel?
Ja, genau so ist es. Kreislaufwirtschaft ist für uns der größte Hebel, um die THG-Emissionen in Scope 3 zu reduzieren. Wie oben beschrieben, haben wir auf diese Emissionen nur indirekt Einfluss, da sie ja in der Lieferkette außerhalb des Unternehmens entstehen. Denn so wie diese Emissionen entlang der gesamten Lieferkette entstehen, sind sie genauso entlang der gesamten Lieferkette am wirksamsten zu reduzieren. Ein Beispiel: Wenn ein Kunststoffunternehmen Post-Consumer-Rezyklate anstatt von Neuware in der Produktion einsetzt, wirkt sich das sowohl auf die eigene Klimabilanz als auch auf die des Kunden positiv aus.
Was bedeutet das für PÖPPELMANN blue®?
Wie ich deutlich machen wollte, ist zur Verwirklichung der Kreislaufwirtschaft der ganzheitliche Blick auf die Aufgaben unabdingbar. Darum ist der Austausch und Dialog mit allen Akteuren in der Wertschöpfungskette elementar wichtig. Wir wollen die Transformationsprozesse in Richtung Kreislaufwirtschaft aktiv vorantreiben. Die Verknüpfung mit der Digitalisierung, zum Beispiel durch die Einführung des Digitalen Produktpasses, kann zukünftig echte Mehrwerte für die interne Organisation, die Lieferkette und die Nachhaltigkeit heben. Wir sind auf jeden Fall bereit, unser Wissen und unsere Kompetenz im Umgang mit dem Material Kunststoff in dieses Ziel einzubringen. Doch das kann nicht allein, sondern nur gemeinsam mit allen Beteiligten gelingen.